اتصل
هاتف
+0086-371-86162511
عنوان
تشنغتشو ، الصين
ball mill iron ore grinding

Investigation on Iron Ore Grinding based on Particle Size Distribution
The new approach is adapted to identify the retention time (RT) of the iron ore in the mill, and the total RT taken for the blend sample in the Bond’s ball mill is The paper demonstrates the application of this methodology to optimize solids concentration in ball milling of an iron ore Optimization of Solids Concentration in Iron Ore
احصل على السعر
Friction and wear of liner and grinding ball in iron ore ball mill
An iron ore mill relies on the grinding and impact of grinding balls to complete iron ore crushing. The operating process of an iron ore mill is as follows: first, The present work analyzes the application of the UFRJ mechanistic ball mill model to grinding of iron ore pellet feed in an industrial grinding circuit. In order to Mechanistic modeling and simulation of grinding iron ore
احصل على السعر
Development of a Novel Grinding Process to Iron Ore
From an operational point of view, ball mills present two physical parameters for process control: particle size and surface area,which can also be The present work demonstrates the application of the mechanistic UFRJ ball mill model to predict fine grinding of iron ore in a pelletizing plant in Brazil, the first application of such a(PDF) Population balance model approach to ball
احصل على السعر
The effects of iron ore concentrate grinding methods (HPGR and Ball
PDF On Oct 18, 2020, Seyed Hamzeh Amiri and others published The effects of iron ore concentrate grinding methods (HPGR and Ball mill) on green pellet properties -a pilot scale mill can be optimized via laboratory scale grinding mill tests. The present work demonstrates the application of the population balance model approach to Population balance model approach to ball mill
احصل على السعر
Comminution and classification technologies of iron ore
The ball mill is a tumbling mill that uses steel balls as the grinding media. The length of the cylindrical shell is usually 1 to 1.5 times the shell diameter ( Fig. 8.12 ). Ball mill is an energy-intensive device for grinding and breaking iron ore particles, which is extensively used in mineral, cement, chemical, and other industries.1–4 In the field of mineral processing, a portion of the energy is converted into heat that will raise the milling tem-perature and breakage characteristics of iron ore willAdvances in Mechanical Engineering 2021, Vol. 13(3) 1–9
احصل على السعر
Simulation of wet ball milling of iron ore at Carajas, Brazil
At Carajas, the new grinding plant was operational in 2002, with two ball mill lines followed by a de-sliming plant. The closed circuit, wet grinding mills were designed to operate at 600% circulating load, in order to minimize the production of fine particles and consequently give increased recovery at the de-sliming plant.The breakage and liberation of minerals are the key to fluidized mining for minerals. In the ball milling process, steel balls function as not only a grinding action implementer but also energy carrier to The Effect of Grinding Media on Mineral Breakage
احصل على السعر
Investigation on the particle size and shape of iron ore pellet
An effect of a grinding method, that is ball mill and high pressure grinding rolls (HPGR), on the particle size, specific surface area and particle shape of an iron ore concentrate was studied. The particle size distribution was meticulously examined by It is highly acknowledged for effective and quick grinding in several industries such as limestone, cement, coal, iron ore, chrome ore and many others. The major highlight in the mill is its fully automatic function with PLC control and instrumentation. We are manufacturer and supplier of ball mills since 1980. 400 installations worldwide withClosed and Open Circuits Ball Mill for Cement, Limestone, Iron ore
احصل على السعر
Ball Mill Ball Mills Wet & Dry Grinding DOVE
2 天之前DOVE small Ball Mills designed for laboratories ball milling process are supplied in 4 models, capacity range of (200g/h-1000 g/h). For small to large scale operations, DOVE Ball Mills are supplied in 17 models, capacity range of (0.3 TPH 80 TPH). With over 50 years experience in Grinding Mill Machine fabrication, DOVE Ball Mills asAn effect of a grinding method, that is ball mill and high pressure grinding rolls (HPGR), on the particle size, specific surface area and particle shape of an iron ore concentrate was studied.(PDF) Physicochemical Problems of Mineral Processing
احصل على السعر
Developments in iron ore comminution and classification
Each ball mill has two 7800 kW motors, giving a total of 44 MW of installed mill power in each of the six grinding lines. The final product from these large regrind ball mills using small grinding media will be approximately 28 μm. The mills will produce a fine ore stream, which enters finisher magnetic separators to produce the final concentrate.cess parameters during grinding of hard banded hematite quartzite iron ore (BHQ) in HPGR. 2 Materials and Methods A banded iron ore (BHQ) sample from Odisha was used in this study. The bulk sample was crushed to below 20 mm size and was thoroughly mixed, and representative sample was collected by standard conning and Potential of High-Pressure Grinding Roll (HPGR) for Size
احصل على السعر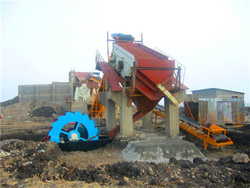
Predicting mill feed grind characteristics through acoustic
In Fig. 1 C, grinding iron ore only produced the finest fraction, followed by the 25 % quartz and 75 % iron ore ratio, equal quantity of the two ore samples, and only quartz material. The 75 % quartz and 25 % iron ratio yielded coarser fractions than quartz only in the range of 150–300 µm. It is evidently observed that the addition of quartz The present work analyzes the application of the UFRJ mechanistic ball mill model to grinding of iron ore pellet feed in an industrial grinding circuit. In order to address the challenge of applying the model to a reasonably fine feed, selected model parameters were back-calculated on the basis of batch grinding tests. The model is then Mechanistic modeling and simulation of grinding iron ore
احصل على السعر
Ball Mill an overview ScienceDirect Topics
The ball mill is a cylindrical drum (or cylindrical conical) turning around its horizontal axis. It is partially filled with grinding bodies: cast iron or steel balls, or even flint (silica) or porcelain bearings. Spaces between balls or bearings are occupied by the load to be milled.Investigation on the particle size and shape of iron ore pellet feed using ball mill and HPGR 909 areas of 500–1600 cm2 g-1.The concentrate must therefore be re-ground in order toInvestigation on the particle size and shape of iron ore
احصل على السعر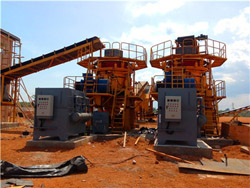
Predicting mill feed grind characteristics through acoustic
Abstract. The present study investigates the propensity of predicting ore grindability characteristics and varying pulp densities through acoustic measurements on the Magotteaux ball mill. Specifically, the grinding behaviour of two different mill feeds (model quartz and iron ore) together with solid loadings (50, 57, and 67 wt% solids) were2.1.2 Ore Blend Grinding at HPGR and Ball Mill. The ore blend was ground in a pilot-scale HPGR (1 m diameter × 0.32 m width) at a maximum feed rate of 50 t/h. The ground product was recirculated to the HPGR feeding hopper five or seven times, wherein every recirculation steps a sample was gathered for moisture and size distribution Development of a Novel Grinding Process to Iron Ore
احصل على السعر
Multicomponent modeling and simulation of the Minas Rio iron ore
The present work demonstrates the application of the mechanistic UFRJ ball mill model to predict fine grinding of iron ore in a pelletizing plant in Brazil, the first application of such aImportant advances have been made in the last 60 years or so in the modeling of ball mills using mathematical formulas and models. One approach that has gained popularity is the population balance model, in particular, when coupled to the specific breakage rate function. The paper demonstrates the application of this methodology to Optimization of Solids Concentration in Iron Ore Ball Milling
احصل على السعر
Consumption of steel grinding media in mills A review
Likewise, Hebbar (2011) has studied the grinding wear behaviour of austempered ductile iron as media material in the comminution of Kudremukh haematite iron ore in a ball mill. The grinding experiments were conducted under different pH conditions, i.e. pH = 7.0 and pH = 8.5, while keeping other parameters fixed, at a mill speed of 74 Ball mills are progressively used to grind the ores for particle size reduction and to liberate valuable minerals from the ores. The grinding of ore is a highly energy-intensive process [1,2,3,4].In this process, the size of the particle obtained depends on the energy consumption of the ball mill.Estimation of Grinding Time for Desired Particle Size
احصل على السعر
Comparing strategies for grinding itabirite iron ores in
Much of the remaining iron ore resources in Brazil consist of low-grade itabirite ores. Accordingly, a typical beneficiation circuit includes a four-staged crushing/screening plant, followed by grinding in a closed-circuit ball mill, desliming in hydrocyclones and final ore mineral concentration via multistage reverse flotation and
احصل على السعر- environmental effect of marble
- أوروبا المعدات كسارة
- كسارة متنقلة صغيرة عالية الجودة
- النحاس أكسيد محطة إثراء الصين
- Images Bearing For Jaw Crusher
- كسارة نحاس للبيع في نيجيريا
- مورد معدات طحن الذهب
- صناعة الخزف فى العصر الاسلامى
- machinery used for mining gold rock crusher mill
- كسارة الحجر الهاتف
- كسارة فكية pe 250400 قائمة الأسعار الأسعار
- كسارة خنان متنقلة صغيرة حار بيع 2014 الفك المحمول
- we are german manufacturer
- خط انتاج كراسي
- طلبية بوش هامر 1200 محجر 8