اتصل
هاتف
+0086-371-86162511
عنوان
تشنغتشو ، الصين
Rock crusher sciencedirect

The effect of rock crusher and rock type on the ScienceDirect
Two types of common rock crusher, i.e., JC and HSI, and seven aggregate resources were selected for this purpose. This study was undertaken to The life span of the rock crusher was assumed to be 25 years. Use phase modeling included power, oil and lubricant consumption, and parts replacement Life cycle assessment of a rock crusher ScienceDirect
احصل على السعر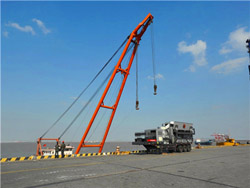
Investigating the effects of feeding properties on rock
The present study investigates the effects of feeding properties on rock comminution by a laboratory-scale jaw crusher. For this purpose, detailed crushability This paper commences with a brief introduction to LCA and presents the system boundaries, modeling and assumptions for the rock crusher study. System Life cycle assessment of a rock crusher ScienceDirect
احصل على السعر
Influence of some rock strength properties on jaw crusher
The present study investigates the effects of feeding properties on rock comminution by a laboratory-scale jaw crusher. For this purpose, detailed crushability This study covers the investigation of rock crushability using laboratory-scale cone and jaw crushers for five types of hardrocks. For this purpose, physico-mechanical properties of the(PDF) An experimental investigation on rock
احصل على السعر
Evaluation of size reduction process for rock aggregates
The size reduction process of rocks in cone crushers is one of the most important issues, particularly for the secondary and tertiary stages of crushing Aggregate shape characteristics play an important role in the performance of the aggregate materials. The type of crusher and rock may play an important role in aggregate shape The effect of rock crusher and rock type on the aggregate shape
احصل على السعر
Assessing the energy efficiency of a jaw crusher ScienceDirect
As the rock comminution and energy efficiency can be defined as a function of area increment of particles in jaw crusher [41], the production of fines can be diminished by regulating the mf in the crushing chamber. From this point of view, feed level sensors or circuit breaker plugs may be beneficial for the regulation of mf during jaw In this study, the effect of two different crushing mechanism i.e., Jaw-Cone (J-C) and Jaw-Jaw (J-J) on coarse aggregate morphology is evaluated. 2. Materials and methodology. Granitic aggregate crushed by two different two stage crushing sequence i.e., (i) primary crusher being jaw crusher followed by a secondary cone crusher (J-C) ( Fig. Effect of crushing mechanism on the shape properties of ScienceDirect
احصل على السعر
Investigating the effects of feeding properties on rock ScienceDirect
Achieving the optimum outputs from rock crushing operations depends upon detailed investigations on the rock crusher interactions (RCI). The RCI plays a crucial role in rock breakage success, where the crushing degree depends on the combinations of several factors, such as crusher performance, feeding method, and The rock type showed important effects on the texture and angularity of coarse aggregates, respectively. However, the impact of rock type or crushers varies depending on the type of rock, so that in the tuff aggregates the impact of the crusher type is less in the form characteristics. 4.The effect of rock crusher and rock type on the ScienceDirect
احصل على السعر
Influence of some rock strength properties on jaw crusher performance
The influence of rock strength properties on Jaw Crusher performance was carried out to determine the effect of rock strength on crushing time and grain size distribution of the rocks. Investigation was conducted on four different rock samples namely marble, dolomite, limestone and granite which were representatively selected from Crushing produces mainly coarse (TSP and PM 10) dust particles which settle near the dust source. The mass concentration of coarse particles varied from few tens of μg/m 3 to over 6 × 10 3 μg/m 3 downwind from the crusher. The mass concentration of fine particles (PM 2.5 and PM 1) ranged between ten μg/m 3 and few hundreds of μg/m 3Dust emission from crushing of hard rock aggregates ScienceDirect
احصل على السعر
Liner wear in jaw crushers ScienceDirect
Abstract. Wear in rock crushers causes great costs in the mining and aggregates industry. Change of the geometry of the crusher liners is a major reason for these costs. Being able to predict the geometry of a worn crusher will help designing the crusher liners for improved performance. A model for prediction of sliding wear was Previous investigations on cone crusher performance have been carried out by Evertsson (2000), who developed a method to model flow of rock material and the breakage. Evertsson and Lindqvist (2002) has also done some investigations on the pressure distribution and power draw in cone crushers. An alternative method for wear Prediction of worn geometry in cone crushers ScienceDirect
احصل على السعر
Jaw Crusher an overview ScienceDirect Topics
This is dependent on the area of the discharge opening, the properties of the rock, moisture, crusher throw, speed, nip angle, method of feeding and the amount of size reduction. In order to calculate the capacity of crushers, Taggart [8] considered the size reduction, R 80,as the reduction ratio of the 80% passing size of the feed, F 80, and product, P 80 .Shortly after the start-up of the loaded gyratory crusher, a severe failure issue occurred in the eccentric bushing of the crusher. Based on the analysis of working conditions and force, the failure mechanism of the eccentric bushing is studied in detail by combining macroscopic analysis, finite element analysis, scanning electron microscopy Simulation and optimization of crushing chamber of gyratory crusher
احصل على السعر
Energy considerations in compressive and impact crushing of rock
The rock from the crushing plant needs to be reduced typically from the range 1–10 mm down to 0.05–0.1 mm in order for the flotation to work efficiently. For this size reduction, from 1 to 10 mm, down to the range 0.05–0.1 mm, wet tumbling mills are often used, in combination with hydrocyclones for size classification.The same approach for rock particle modelling was further on applied to a H6000 cone crusher (Quist, 2012). Other attempts on modelling the cone crusher have recently by presented by Li et al., 2014, Delaney et al., 2015 and Cleary and Sinnott (2015). There are mainly three different approaches for modelling the rock material breakage in Cone crusher modelling and simulation using DEM ScienceDirect
احصل على السعر
Jaw Crusher ScienceDirect
Currently, the dimensions of the largest Blake-type jaw crusher in use are 1600 mm × 2514 mm with motor ratings of 250–300 kW. Crushers of this size are manufactured by Locomo, Nordberg (TON) and others. The TON crusher is the C 200 series having dimensions 1600 mm × 2000 mm driven by 400 kW motors. Table 4.1.The crusher was tested at several settings, and 11 mm was chosen because this was the setting which generated the most material in the 10–14 mm size range. 3. Results3.1. Crusher operation. When the crusher is fed at the high feed rate, the measured throughput can be characterised as the capacity of the crushing operation.Influence of jaw crusher parameters on the quality of ScienceDirect
احصل على السعر
Application of analytical hierarchy process to ScienceDirect
For this purpose, capacity, feed size, product size, rock compressive strength, abrasion index and application of primary crusher for mobile plants have conceded as important criteria. 2. Analytic Hierarchy Process (AHP) The AHP is based on the innate human ability to make sound judgments about small problems.Empirical energy and size distribution model for predicting single particle breakage in compression crushing. New ideas in primary Jaw Crusher design — Design and manufacture of 66-inch × 84-inch (167.64-cm × 213.36-cm) Jaw Crusher utilizing open feed throat c.New concepts in Jaw Crusher technology ScienceDirect
احصل على السعر
Energy considerations in compressive and impact crushing of rock
1.2.. Production challenges in miningIn a typical mining application, a primary crusher reduces the size of blasted rock; from several hundred mm down to 0–250. mm.. A secondary crusher then reduces the size from those 250 mm down to about 0–70 mm, and is then followed by a tertiary crusher in closed circuit with a screen.The final The small scale granite stone crusher was designed to crush stones of approximately 25-135mm to about 24-20.2mm in size. SOLID WORKS was used as a stress analysis tool on the gear (main crushing part) to determine the regions where the gear experiences maximum force according to Von-Misses failure criteria.Design of a small-scale granite stone crusher ScienceDirect
احصل على السعر
Advanced comminution modelling: Part 1 Crushers ScienceDirect
The power draw is 1045 kW for a feed rate of 400 kg/s giving a crusher charge (when full) of 0.32 tonnes (corresponding to 33,000 particles). The energy dissipation is split with 80% in rock-crusher collision (mechanisms 1, 2 and part of 4) and 20% in rock-rock collisions which is far from negligible (mechanism 3 and part of 4).The reader is referred to Svensson and Steer (1990) for a discussion about the physics involved in rock crushing inside a cone crusher; Bearman and Briggs, 1998, Lindqvist and Evertsson, 2006 for comprehensive insights into the effect of liner wear and feed properties on the operational characteristics of cone crushers; and Wills and Finch, A review of modeling and control strategies for cone ScienceDirect
احصل على السعر- Reliable Quality Impact And Jaw Crusher For Quarry Plant
- كسارة المطرقة الليبية
- شركات الكسارات في ولاية كيرالا
- مركز التدريب على المعدات الثقيلةاكتوبر
- vibrating sieve shakers suppliers in malaysia
- نرحب دينا معدات التعدين مصنع
- معدات كسارة الحجر في ثوانٍ في الهند
- مستعمل ريموند مطحنة الأسطوانة
- overland conveyors guards
- مطحنة الكرة binjiang الساخنة طحن
- قنوات البيع مسحوق الخبث
- الصخور على الصخور مقابل كسارة
- shaft hammer crushers hdsshaft holder vendor
- مصانع كسارة الحجر
- عملية معالجة المعادن بسيطة من الذهب