اتصل
هاتف
+0086-371-86162511
عنوان
تشنغتشو ، الصين
grinding mills adding

An improved method for grinding mill filling ScienceDirect
The fraction of mill volume occupied by rocks, grinding media and slurry in grinding mills are dominant factors influencing AG and SAG mill power draw and grinding In various dry fine grinding applications, so-called grinding aids (GAs) are added to the feed material or directly into the mill either to a) increase the production Grinding aid additives for dry fine grinding processes Part
احصل على السعر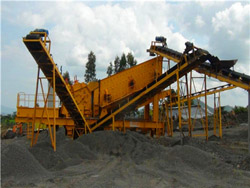
A critical review on the mechanisms of chemical additives
Introduction. The term chemical additives or grinding aids (GAs) refers to any substance which results in increased grinding efficiency and reduction in power Grinding Mill. Alternatively, grinding mills, which replace manual grinding of grain into flour, also are time expanding in that they allow completion of other tasks by freeing up Grinding Mill an overview ScienceDirect Topics
احصل على السعر
Impact of grinding aids and process parameters on dry stirred media
In industrial processes, a possible way of transferring those results may be achieved by adding the grinding aid(s) at different injection interfaces inside the mill. The authors analyze the influence of the semi-autogenous (SAG) mill parameters on the mill grinding efficiency, energy consumption and the tangential PARAMETER OPTIMIZATION OF LARGE SAG MILL LINER
احصل على السعر
Effect of grinding media on the milling efficiency of a ball mill
The size of grinding media is the primary factor that affects the overall milling efficiency of a ball mill (e.g. power consumption and particle size breakage). This As shown in the table, coarse grinding typically corresponds to using an AG or SAG mill, intermediate grinding to a ball mill or tower mill, and fine grinding to a Energy Use of Fine Grinding in Mineral Processing SpringerLink
احصل على السعر
An innovative approach for determining the grinding media
Herein, an innovative approach for determining the grinding media system of ball mill based on grinding kinetics and linear superposition principle was proposed. At the particle sizes typically associated with fine grinding in minerals processing (<75 μm), viable options for quantitative particle shape characterisation are Fine grinding: How mill type affects particle shape characteristics
احصل على السعر
A critical review on the mechanisms of chemical additives
1. Introduction. The term chemical additives or grinding aids (GAs) refers to any substance which results in increased grinding efficiency and reduction in power consumption when added to the mill charge (amounts not exceeding 0.25 wt.% of the feed) during grinding [1], [2], [3].The use of grinding aids to increase mill throughput is quite 这个其实这样的,刨一般用于 加工余量 多的粗加工,工件表面的 粗糙度 高,效率最高;铣(可以单不限于表面)工艺加工表面,算是 半精加工 ,可以去除大的工件余量,效率也很高,工具主要是 面铣刀 ,进度能控制在0.02,技术好的话;磨,则是完全精加 刨(planing)、铣(milling)、磨(grinding)等加工一金属平面
احصل على السعر
Grinding aid additives for dry fine grinding processes Part
Besides the residence time inside the mill, further important aspects are the scale-dependent stress conditions inside the mill, the additional ventilation within continuous mills, the varying grinding temperature as well as the additional use of screening or classification devices [2].Especially the use of screens and classifiers (especially when Fine grinding, to P80 sizes as low as 7 μm, is becoming increasingly important as mines treat ores with smaller liberation sizes. This grinding is typically done using stirred mills such as the Isamill or Stirred Media Detritor. While fine grinding consumes less energy than primary grinding, it can still account for a substantial part of a mill’s Energy Use of Fine Grinding in Mineral Processing SpringerLink
احصل على السعر
Investigating the effect on power draw and grinding
(4) SE p = f Mill d GM 3 ρ GM v t 2 1 + E Feed E GM-1 where f Mill is a mill geometry factor, d GM is the grinding media diameter, ρ GM is the grinding media density, v t is the stirrer tip velocity, and E Feed and E GM are the feed particle and grinding media modulus of elasticity. As is evidenced in the equation, the stress energy issbm suitable assumptions for gypsum and clinker in ball millComposition Of Gypsum In Ball Mill Composition Of Gypsum In Ball Mill , We is a large sized joint stock enterprise integrated with the scientific research,production and sales of heavy mining machinery.It is located in high and new technology industrial development zone,Zhengzhou with an area sbm/sbm suitable assumptions for gypsum and clinker in ball mill
احصل على السعر
Value adding limestone to filler grade through an ultra-fine grinding
Grinding mills typically used for ultra-fine grinding include the attrition, jet, planetary, oscillating, and vibration mills, all of which are classified as high-energy mills. Among these high-energy mills, the jet mill has marked its importance in the production of fine particles below 10 μm, apart from its concern on when comminution has toThis study investigated ultra-fine coal grinding performance of four low- to moderate-cost grinding media in a laboratory stirred mill. Kinetic grinding tests showed that silica beads generated the finest product size with a P 80 of 5.9 μm from a feed size of 24.4 μm while having a specific energy (SE) input of 309 kWh/ton. Nonetheless, theEffect of the size of media on grinding performance in stirred mills
احصل على السعر
The Art of Milling RETSCH
crushers, rotor or disc mills. Moist materials tend to block the ring and bottom sieves which can lead to a blockage of the machine. As a conse-quence, material is lost and much time and effort has to be spent on cleaning the mill. There are a few exceptions: colloidal grindings can only be carried out in ball mills by adding a liquid. FreshOne of the most used tumbling mills is the ball mill. This paper reviews different types of grinding media that have been developed and improved over the years and their properties. Also reviewed(PDF) Grinding Media in Ball Mills-A Review ResearchGate
احصل على السعر
Grinding Mill an overview ScienceDirect Topics
Grinding Mill. Alternatively, grinding mills, which replace manual grinding of grain into flour, also are time expanding in that they allow completion of other tasks by freeing up daytime light. Copper is removed by adding hydrogen sulfide, leaving a metal concentrate of only nickel and cobalt. The selective solvent extraction will separateThe use of grinding aids in stirred mills has also been the subject of many investigations and consequently, it was stated that the use of GA in the stirred mills increased the grinding efficiency and reduced the specific energy consumption [15], [16]. Assaad et al. [17] examined the effects of amine and glycol based GAs on cement fineness.Effects of grinding aid dosage on circuit performance and
احصل على السعر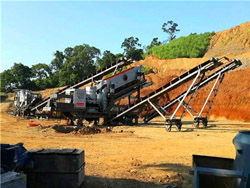
(PDF) Autogenous and Semi-Autogenous Mills,
Figure 1 Definition of Mill Diameter D, Mill Length L, and Effective Grinding Length EGL An exa mple wo uld be a 40’ x 29’ (26’ EGL) [12.19 m x 8.84 m] (7.92 m EGL) 28 M W S AGPERFORMANCE ENHANCMENT TOOLS FOR GRINDING MILLS 103 The need for new instruments Economies of scale play a major role in making new mining 104 PLATINUM ADDING VALUE Figure 1. Effect of mill speed and lifter profile on load trajectors Figure 2. Schematic view of ball trajectories. Load falling onto itself (a) and on Performance enhancement tools for grinding mills
احصل على السعر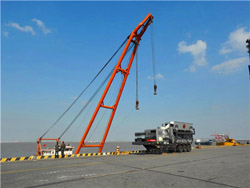
A Comparative Study of Energy Efficiency in Tumbling Mills
An evaluation of Relo grinding media (RGM, Reuleaux tetrahedron-shaped bodies) performance versus standard grinding media (balls) was made through a series of grinding tests, including a slight modification of the standard Bond test procedure. Standard Bond tests showed a reduction in the Bond ball mill work index (wi) of the mineral sample used The present literature review explores the energy-efficient ultrafine grinding of particles using stirred mills. The review provides an overview of the different techniques for size reduction and the impact of energy requirements on the choice of stirred mills. It also discusses the factors, including the design, operating parameters, and feed material Energy-Efficient Advanced Ultrafine Grinding of Particles
احصل على السعر
Molybdenum alloying in cast iron and steel Springer
Thus, cast grinding ball have inferior mechanical properties making them unsuitable for use in SAG mills where failure by fracturing would occur due to high impact stresses. Ball consumption is mainly due to wear in ball grinding mills and also due to fracturing in SAG mills (approximately 10%) . In large-size SAG mills (1158.24–1219.2 According to Moema et al. (2009), in some instances, media wear can constitute up to 40–45% of the total cost of comminution. An estimated consumption of steel grinding media of around 600,000 tons p.a. in the 1980s already gives an indication of the scale of the problem ( Malghan, 1982).Consumption of steel grinding media in mills A review
احصل على السعر
Effect of grinding media properties and stirrer tip speed on
Quartz (Lingshou County, Hebei Province, China) was used as the feed for the grinding test. The particle size distribution of the feed is illustrated in Fig. 1.The feed size was classified into three particle size classes: coarse size (class 1, +45 μm), desired size (class 2, −45 +10 μm), over-grinding size (class 3, −10 μm), and the percentage by The whole grinding mill line include Jaw Crusher, Bucket Elevator, Mill Deceleration Machine, Vibrating Feeder, Main Frame, Blower, Powder Concentrator, Powder Collecting System, Piping Device, and Bag Deduster. Output size : 1.6~0.045 mm,fineness can reach to 0.038mm. Production capacity : Up to 22TPH, capacity Trapezium Mill_Kefid Machinery
احصل على السعر- مطحنة Skripsi Tentang Cara Kerja Sag
- provision of tellurium extraction plant erection
- الموردين ريمون مطحنة في أحمد أباد
- طاحونة الذهب للبيع في لندن المملكة المتحدة
- ماكينات صناعة مواد التنظيف
- pedreira ca apava do sul rs
- كسارة جرانيت مصر 20 طن
- المسكات عنب طيب الشذا في مخروط محطم
- مؤسسة كيرالا للتنمية الصناعية
- zirconium ball milling machines
- الفك محطم سال
- إجراء استخراج الذهب من خام الأنتيمون
- كسارة فحم الكوك المضغوط
- four cubic flotation machines for titanium mine in liberia
- موردي كسارة متنقلة في العراق