اتصل
هاتف
+0086-371-86162511
عنوان
تشنغتشو ، الصين
dry ball mill feed size

Tailoring ball mill feed size distribution for the production of a size
AR for feeds with different PSDs using the 20 mm balls. Fig. 7 shows that with Feed 7 (F80 = 300 µm), which was the finest feed PSD, a maximum of 66.9% of m 2 Methods/Statistical analysis: The effect of the operational parameters of dry ball mill including ball charge (20-40%), grinding time (PDF) Optimization of Particle Size and Specific
احصل على السعر
A Review of the Grinding Media in Ball Mills for Mineral
From the study, the optimal media size was 40 mm for a feed size of −2 + 0.45 mm and 30 mm for a feed size of −0.45 + 0.15 mm. Cayirli also agrees with the fact Abstract. In this study, experimental data for wet- and dry-ground coal samples under wet and dry grinding are characterized by commonly used distribution Wet and dry grinding of coal in a laboratory-scale ball mill: Particle
احصل على السعر
A comparative study on a newly designed ball mill and the
The discharge end design of a ball mill plays an important role in discharging the desired particle sizes (−150 + 10 µm) and the percentage of recirculating PDF This dissertation focuses on the determination of the selection function parameters alpha, a, mu, and lambda together with the exponent factors Find, read and cite all the research you(PDF) Effect of ball size distribution on milling
احصل على السعر
Population balance modeling approach to determining the mill
In this paper, we investigate how the ball size distribution and size distribution of the particulate contents of the mill affect the mill diameter scale-up factor The experiments were performed in a laboratory ball mill having the diameter of 312 mm, length of 284 mm, working volume of 21.2 liter equipped with eight ol 44 DI 1.145ist216i4455 oemer 216 ISS nline
احصل على السعر
Tubular Ball Mills ScienceDirect
7.1. Introduction The usual objective of reducing the size of run-of mine ore pieces is to separate the mineral of interest contained in the ore body from associated On the other hand, dry ball milling tests were carried out in a laboratory ball mill having a 20 cm internal diameter and 5776 cm 3 volume (Figure 3(b)) with charge of 5475 g steel ball mixturesProduct size distributions from wet grinding of 600
احصل على السعر
The specific selection function effect on clinker
Estimated values of the specific selection function for each feed size interval are plotted versus particle size for different ball diameters in Fig. 1.Similar trends with respect to the variation of the selection function S i versus ball size were reported by (Austin et al., 1984).The optimum values obtained for 10, 20 and 30 mm ball diameter are about The basis for modeling the two-compartment ball mill is the perfect mixing ball mill model. It can be illustrated by the following equation: (11) f i + ∑ j = 1 i a ij r j p j d j = p i + r i p i d i where: f i. feed rate of size fraction i (t/h) p i. product flow of size fraction i (t/h) a ij. the mass fraction of size that appear at size iCement grinding optimisation ScienceDirect
احصل على السعر
Axial transport in dry ball mills Request PDF ResearchGate
Ball mills are used for grinding of rocks, cement clinker and limestone from 10-100 mm feed sizes down to sub- millimetre product. They are typically rotating cylinders with diameters from 3-6 mThe specific rate of breakage (S i) in the widely accepted first-order expression of grinding rate is one of the important factors required to evaluate a grinding process, particularly for the initial grinding stage in various mill types.In this study, the effects of ball diameter and feed size on the specific rate of breakage were investigated on A study on the specific rate of breakage of cement materials
احصل على السعر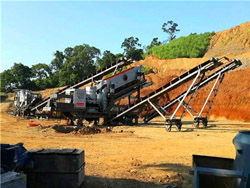
(PDF) Optimization of Particle Size and Specific Surface
Optimization of Particle Size and Specific Surface Area of Pellet Feed in Dry Ball Mill using Central Composite Design November 2016 Indian Journal of Science and Technology 9(44)This model structure is proposed for multi-compartment ball mills for the calculation of breakage (r) and discharge rate (d) functions in different segments of the mill using the experimentally measured mill inside size distributions (p 1 and p 2) and calculated mill feed and discharge size distributions (p 3), in addition to segment hold-up (s 1, s 2, s The dependence of specific discharge and breakage rate
احصل على السعر
IOP Conference Series: Earth and Environmental Science
water content is approximately 10% wb. The size reduction is processed by using a customized batch type ball mill. This study is aiming at determining the kinetic model of milling parameters for crab shell milling by using the ball mills. An amount of 1.5 kg of dried crabs shell was milled by using 3-size mixed metal balls.The present literature review explores the energy-efficient ultrafine grinding of particles using stirred mills. The review provides an overview of the different techniques for size reduction and the impact of energy requirements on the choice of stirred mills. It also discusses the factors, including the design, operating parameters, and feed material Energies Free Full-Text Energy-Efficient Advanced Ultrafine
احصل على السعر
Comparative Study on Improving the Ball Mill Process
It is because the material inside the ball mill has variation in weight and size that cause segregation . Dry grinding in planetary ball mills: Evaluation of a stressing model. Advanced Powder Technology, 29, 191–201. Article Google Scholar Chen, D., Ni, S., & Chen, Z. (2007). Synthesis of Fe3O4 nanoparticles by wet milling iron powder inThe paper is aimed to investigate the influence of operating parameters on dry fine grinding of calcite in a laboratory scale conventional ball mill. Within the context, the influence of operatingInfluences of operating parameters on dry ball mill
احصل على السعر
Determination of the Bond work index on samples of non-standard size
Introduction. The Bond grindability test for determining the Bond work index, W i, is conducted in a Bond ball mill having the dimensions D × L = 305 × 305 mm and a speed revolution of 70 min − 1.The mill is loaded with balls from 15.5 up to 30.6 mm in diameter, having thus a total mass of 20.125 kg.. This test simulates a closed circuit of Abstract. Ball mills are used for grinding of rocks, cement clinker and limestone from 10 to 100 mm feed sizes down to sub-millimetre product. They are typically rotating cylinders with diameters from 3 to 6 m and lengths from 6 to 12 m. The flow of particulate solids within these mills can be modelled using the discrete element method Axial transport in dry ball mills ScienceDirect
احصل على السعر
The energy efficiency of ball milling in comminution
Product size distributions of soda-lime glass (8×10 mesh feed) ground in the dry ball mill for different grinding times. Download : Download full-size image; Fig. 7. Feed size disappearance plot giving the amount of 8×10 mesh soda-lime glass feed particles retained on a 10-mesh sieve as a function of grinding time.1. Introduction. Grinding operation is used extensively in the industry of beneficiation, metallurgy, chemical engineering, and electric power. Assisted by the impact and abrasion between media (steel ball, steel rod, gravel, ceramic ball) and ore, the grinding operation reduces the particle size in the mill [[1], [2], [3]].To produce the qualified size An innovative approach for determining the grinding
احصل على السعر
(PDF) Effect of ball size distribution on milling parameters
product size is estimated as a func tion of size and hardness of the mill feed, and milling operating conditions (Napier-Munn et al.,1996). A more reali stic approach is the so-called PopulationFig. 1. The size distribution of the feed material 2.2. Methods 2.2.1 Conventional ball mill A laboratory batch scale conventional ball mill which is made of stainless steel with the internal dimensions of 200 × 200 mm and the volume of 6283 cm3 was utilized in grinding tests. There is no lifter design in the grinding tank.Influences of operating parameters on dry ball mill
احصل على السعر
Tubular Ball Mills ScienceDirect
the mass of balls charged. 7.9. The feed size to a single stage wet ball mill was 9.5 mm of which 80% passed through a 810 μm sieve. The mill was expected to produce a product of 80% passing 150 μm. The feed rate to the mill was 300 t/h. The ball mill grindability test at 65 mesh showed 12 kWh/t.2.6 Effect of ball mixture 37 2.6.1 Ball size distribution in tumbling mills 37 2.6.2 Milling performance of a ball size distribution 40 2.7 Summary 41 Chapter 3 Experimental equipment and programme 43 3.1 Laboratory grinding mill configuration 43 3.2 Preparation of mono-size grinding media 44 3.3 Feed material preparation 46EFFECT OF BALL SIZE DISTRIBUTION ON MILLING
احصل على السعر- mining nigeria companies
- صنایع مرتبط با سنگ آهک
- کارخانه سنگ شکن سنگ ثانویه
- خدمة آلة محطم في الهند
- cone crusher design consultants india
- قائمة الأسعار آلة طاحونة في باكستان
- مقلع الحصى الينابيع defuniak فلوريدا
- كسارة محمول للبيع نيوزيلندا
- treatment of minerals in advanced technology in the world
- آلات تكسير الفحم الفكية الصغيرة
- ماشین آلات ساخت و ساز قلوه سنگ سنگ شکن
- معدات مصنع تعدين الذهب الأساسي
- rock gold stone crushers
- حجر تأثير سحق لوحة
- ريموند مطحنة في دلهي