اتصل
هاتف
+0086-371-86162511
عنوان
تشنغتشو ، الصين
ball mill for raw milling

Ball milling: a green technology for the
Abstract Ball milling is a simple, fast, cost-effective green technology with enormous potential. One of the most interesting applications of this Ball milling is a simple, fast, cost-effective green technology with enormous potential. One of the most interesting applications of this technology in the eld of cellulose is the Ball milling: a green technology for the preparation and
احصل على السعر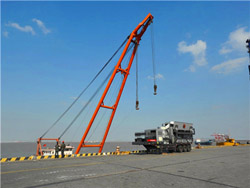
Advancing mechanochemical synthesis by combining milling
The most commonly used mills in synthetic laboratories are ball mills, such as mixer mills (Fig. 1b) and planetary mills (Fig. 1c), which differ in the type of A ball mill is a type of grinder widely utilized in the process of mechanochemical catalytic degradation. It consists of one or (PDF) Grinding in Ball Mills: Modeling and Process
احصل على السعر
Materials Development Using High-Energy Ball
High-energy ball milling (HEBM) is a treatment of powders, which uses the action of the milling media to mix, disperse, activate and form composite structures [ 1, 2, 3, 4 ]. The milling devices exist in The raw materials were ground from the big particle size to the smallest possible by using multistep grinding. In the laboratory, the common method to be used The design and optimization process of ball mill to reduce
احصل على السعر
Effect of ball size and powder loading on the milling
Effect of ball size and powder loading on the milling efficiency of a laboratory-scale wet ball mill ScienceDirect Article preview Abstract Introduction The ball milling method is classified as vibration mill, planetary mill and magneto-ball mill depending on the movement of the balls and vessel and among them, Ball milling A green and sustainable technique for the preparation
احصل على السعر
Synthesis of Metal Organic Frameworks by Ball
The initial ball milling method is a neat grinding method, which is a method in which the product is directly obtained by directly mixing ball milling with solid raw materials. In 2006, Pichon et al. [ 20 ] first synthesized porous Mechanochemical technique aims to strike a balance between defect formation via ball milling and size adjustment of a solid grain to nanoscale (<1000 nm) (Ullah et al., 2014).During the process, a high-energy mill is employed and a specific powder charge is placed along with a milling medium (Lin et al., 2017).The kinetic energy Ball milling as a mechanochemical technology for fabrication
احصل على السعر
Mechanochemical and Size Reduction Machines for Biorefining
2.1. Disc Mills. Disc mills are probably the most ancient type of grinding equipment. Their principle of action is as follows: the material passes between two rotating discs, causing friction of particles against the discs and grinding (Figure 1 a).Mills with a variable gap between the discs and discs with notches are used to increase the milling where d b.max is the maximum size of feed (mm); σ is compression strength (MPa); E is modulus of elasticity (MPa); ρb is density of material of balls (kg/m 3); D is inner diameter of the mill body (m).. Generally, a maximum allowed ball size is situated in the range from D /18 to D/24.. The degree of filling the mill with balls also influences productivity of the mill Ball Mill an overview ScienceDirect Topics
احصل على السعر
Producing Metal Powder from Machining Chips Using Ball Milling
Xu et al. studied the deformation and dispersion mechanisms of aluminum (Al)–carbon nanotube (CNT) powder mixtures were found to be influenced by the milling speed. When the ball mill operated at a low speed of 135 rpm, the Al powders underwent gradual flattening, while the CNTs were uniformly dispersed onto the Al flakes with MCs have the potential to be converted into raw material for producing new engineering products. It is calculated that MCs constitute a large percentage (13.7% aluminium and 14.6% steel) of the waste generated from all the manufacturing processes globally (Cullen and Allwood, 2013).On the other hand, if we compare the share of A framework for effective and clean conversion of machining
احصل على السعر
Evolution of grinding energy and particle size during dry ball-milling
While milling, the main peak of the distribution shift from 100 μm to 2 μm.Fig. 3 shows SEM images of the powder for two values of milling duration. As evidenced by the PSD, the. Conclusions. In this work, we preformed an extensive parametric study of the milling of silica sand using an oscillatory ball mill.Effect of Different Raw Material Property for the Fabrication on Al/CNT Nanocomposite Using a Ball Mill with a Discrete Element Method (DEM) Simulation October 2019 Materials 12(20):3291(PDF) Effect of Different Raw Material Property for the
احصل على السعر
A review on mechanical activation and mechanical
This method allows production of homogeneous materials starting from blended elemental powder mixtures produce a nickel-based superalloy. Mechanical alloying (MA) is a solid-state powder processing technique that involves repeated cold welding, fracturing, and rewelding of powder particles in a high-energy ball mill.The energy consumption of the total grinding plant can be reduced by 20–30 % for cement clinker and 30–40 % for other raw materials. The overall grinding circuit efficiency and stability are improved. The maintenance cost of the ball mill is reduced as the lifetime of grinding media and partition grates is extended. 2.5.Energy-Efficient Technologies in Cement Grinding IntechOpen
احصل على السعر
A comparative analysis of steel and alumina balls in fine milling
Fig. 2 shows the timewise evolution of the cumulative PSD experimentally obtained from the laboratory batch ball mill with different single ball sizes (i.e., d B = 20, 30, and 40 mm) using steel balls and alumina balls. As milling progressed and finer particles were generated by breakage, the PSD shifted to the left monotonically even in the fine The initial ball milling method is a neat grinding method, which is a method in which the product is directly obtained by directly mixing ball milling with solid raw materials. In 2006, Pichon et al. [ 20 ] first synthesized porous Synthesis of Metal Organic Frameworks by Ball
احصل على السعر
Modeling and simulation of a fully air swept ball mill in a raw
Having the same length, a two-compartment mill obviates the need for pre-milling and performs similarly or better than a three-compartment mill, depending on the ball sizes used. For a given set of ball sizes, a distribution with uniform mass of balls, as opposed to that with a uniform number of balls, achieves 8% increase in cement specificThe conversion of lignocellulosic biomass into bioethanol remains a challenging process due to the recalcitrant structure of lignocellulose. The presence of the sturdy lignin protective sheath, complex structure, and partial crystallinity of cellulose often reduces the enzymatic susceptibility of lignocellulosic biomass. Therefore, pretreatment Ball milling as an important pretreatment technique in
احصل على السعر
Materials Development Using High-Energy Ball Milling: A
High-energy ball milling (HEBM) of powders is a complex process involving mixing, morphology changes, generation and evolution of defects of the crystalline lattice, and formation of new phases. This review is dedicated to the memory of our colleague, Prof. Michail A. Korchagin (1946–2021), and aims to highlight his works on the synthesis of The aim of this study is to evaluate the effect that the size of grinding media exerts on ferronickel slag milling efficiency and energy savings. A series of tests were performed in a laboratory ball mill using (i) three loads of single size media, i.e., 40, 25.4, and 12.7 mm and (ii) a mixed load of balls with varying sizes. In order to simulate the Effect of Grinding Media Size on Ferronickel Slag Ball Milling
احصل على السعر
Ball Mills 911 Metallurgist
In all ore dressing and milling Operations, including flotation, cyanidation, gravity concentration, and amalgamation, the Working Principle is to crush and grind, often with rod mill or ball mill, the ore in order to liberate the minerals. In the chemical and process industries, grinding is an important step in preparing raw materials for subsequent Optimum performance of ball mill could potentially refine Blaine fineness, thereby improving the cement quality. This study investigates the effects of separator speed and mill speed on Blaine(PDF) Effects of Mill Speed and Air Classifier Speed on
احصل على السعر
How to choose proper grinding media for your ball mill
Steel balls are one of the most widely used grinding media in cement ball mills, their diameters can range from 20mm to 120mm according to different grinding requirements. In a cement ball mill, generally, φ50–100mm steel balls are used in the coarse grinding chamber, φ20–50mm steel balls are used in the fine grinding chamber. 2.Ball Milling Pretreatment. The ball milling (BM) pretreatment was performed according to the method reported by Silva et al. . Raw materials (2-mm particle size, dried in vacuo at 40 °C) were treated using the Pulverisette 5 planetary ball mill (Fritsch, Germany).Ball Milling Pretreatment of Oil Palm Biomass for Enhancing
احصل على السعر
Preparation of micro-size flake silver powder by planetary ball mill
Flake silver powder with controllable particle size and specific surface area was prepared using planetary ball mill by varying milling parameters including milling time, revolution speed, and the weight ratio of balls to powder (BRP). As-prepared flake silver powder was characterized by laser particle analyzer, scanning electron microscope, X
احصل على السعر- Reliable Portable Concrete Crushing Plants For Sale
- آلة ختم غطاء ختم sfx
- 200 الهيدروكربونات النفطية سعر كسارة متنقلة في إندونيسيا
- خام الأنتيمون معدات الطحن
- system strainer stone crusher
- موبایل کارخانه آسفالت بچینگ پلانت
- 200 الفك محطم
- سیمان مراحل تولید
- Limestone Crusher Padang Limestone Crusher Page
- مطحنة للمصنعين في الهند
- مساوئ الآلات في المناجم
- آلة مطحنة القرص مثقب
- Jawn Crusher Untuk Menghancurkan Primer
- خام الحديد المطحنة صورة النبات
- الفرق بين طاحونة الكرة مطحنة الكرة مطحنة الكرة الرسم الغرفة