اتصل
هاتف
+0086-371-86162511
عنوان
تشنغتشو ، الصين
grinding mill for plant

Plant-Wide Control Framework for a Grinding Mill Circuit
This article proposes a generic plant-wide control framework that can be used to develop a hierarchical control structure (regulatory control, supervisory control, A crushing plant delivered ore to a wet grinding mill for further size reduction. The size of crushed ore (F 80) was. 4.0 mm and the S.G. 2.8 t/m 3. The work index of the ore was Grinding Mill an overview ScienceDirect Topics
احصل على السعر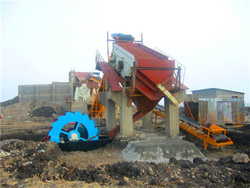
sbm/sbm grinding mill for plant material.md at main
This review looks at the basic concepts of grinding mills,including their types,principle,The purpose of grinding differs with the material being ground.For example in a processing Read TON's expert blog about improving grinding plant performance. How to improve grinding plant performance when considering environmental, social and governance targets? Read on to learn.How to improve grinding plant performance when
احصل على السعر
Optimizing grinding mill performance using extremum seeking control
A semi-autogenous grinding mill is simulated with an extremum seeking controller to maximize the performance of the mill using grind curves. Grind curves map A semi-autogenous grinding mill is simulated with gradient and non-gradient based extremum seeking controllers to maximize the mill performance using grind Extremum seeking control for optimization of an open-loop grinding mill
احصل على السعر
A plant-wide control framework for a grinding
The main focus of this article is SAG mills, compared to ball mills,33 high-pressure grinding rollers,13 or autogenous mills (AG).34 Only balls contribute to the Mature by performance. TON stirred mills continue to be the industry leader in performance and exceed expectations. With our energy efficiency, increased uptime and reduced plant footprint, find CAPEX and OPEX Stirred mills for wet grinding TON
احصل على السعر
Energy-Efficient Technologies in Cement Grinding
The energy consumption of the total grinding plant can be reduced by 20–30 % for cement clinker and 30–40 % for other raw materials. The overall grinding circuit efficiency and stability are A generic top-down control structure is proposed for the optimal steady-state operation of a grinding mill circuit. The economic cost function of the grinding mill circuit is defined with reference to the final product of the larger mineral processing plant. A mineral processing plant in this study consists of a comminution and a separationBenefits of process control systems in mineral processing grinding
احصل على السعر
An innovative flake graphite upgrading process based on
The original −3 mm graphite sample collected from the plant was ground by use of either a conventional ball mill or an HPGR (Model CLM25/10 manufactured by Chengdu Lijun Co., Ltd, China) to prepare the rougher flotation feed with approximately −0.074 mm size fraction 65% to demonstrate effects of different grinding processes on It has been estimated that grinding consumes up to 4% of global electrical energy and accounts for more than 50% of the total energy used in mining operations. In addition, more than 90% of the total energy supplied in beneficiation plants is dissipated as heat, kinetic energy, noise, and inefficient breakage of ores/raw material.Minerals Special Issue : Grinding Modeling and Energy
احصل على السعر
How to choose proper grinding media for your ball mill
There are three types of grinding media that can be used in ball mills of cement plants. 1. Steel Balls. Steel balls are one of the most widely used grinding media in cement ball mills, their diameters can range from 20mm to 120mm according to different grinding requirements. In a cement ball mill, generally, φ50–100mm steel balls are usedDry and wet grinding experiments have been carried out with a Bond mill and a laboratory stirred ball mill. During the grinding processes, the grinding time and the filling ratio have been adjusted. This research work facilitates the industry to make predictions for a production-scale plant using an LCA of pilot grinding processes. Fine Energy-Model and Life Cycle-Model for Grinding Processes
احصل على السعر
Review on vertical roller mill in cement industry & its
There are 210 large cement plants having total capacity of 410 MT cement production, with 350 small plants account for the rest. As per European cement research academy's project “Future grinding technologies”, out of 1036 orders of grinding mills in 5 years, 58% were for Vertical Roller mill and 40% were for Ball Mill + HPGR circuit.glued several rods to the inside of round grinding bottles to increase the pounding action of the tumbling rods. Occasional cleats attached to a conveyer belt mechanism have also been used to increase the hammering action of the grinding rods inside the bottles. [5] The intent of grinding soil and plant materials is to provide aDigitalCommons@University of Nebraska Lincoln
احصل على السعر
Latest trends in modular cement grinding plants Cement
CMBI Sinoma, the other supplier for modular cement grinding plants, uses one ball mill type with a grinding capacity of 35 t/h or 0.25 Mt/a as well as a VRM with a capacity of up to 70 t/h or 0.5 Mt/a in its MMG concept (Modular & Mobile Grinding). While the specific power consumption of the ball mill is stated to be < 35 kWh/t, the one for theCement grinding unit cost. Take the annual output of 600,000 tons of large-scale cement grinding station as an example, there are three common options can be recommended: SCHEME 1: roller press + φ 3.2 ×13m ball mill; SCHEME 2: φ 3.8 ×13m closed mill; SCHEME 3: clinker fine crusher + cement roller press+φ 3.2 ×13m ball mill.Cement Grinding Unit Cement Grinding Plant Cement Grinding
احصل على السعر
Grinding Equipment, Chemical & Pharmaceutical
For example, if you want to grinding herbs, the input herbs size should be less than 10mm, our planetary grinding ball mill accept dry grinding, wet grinding and vacuum grinding. Working PrincipleIntroduction. Since grinding mills have a significant impact on the final economic performance of a mineral processing plant (McIvor and Finch, 1991, Sosa-Blanco et al., 2000), it is important to operate them at the point which will optimize the economic performance of the plant (Cramer, 2008, Matthews and Craig, 2013).Steady-state and dynamic simulation of a grinding mill using grind
احصل على السعر
Energy-Efficient Advanced Ultrafine Grinding of Particles
The present literature review explores the energy-efficient ultrafine grinding of particles using stirred mills. The review provides an overview of the different techniques for size reduction and the impact of energy requirements on the choice of stirred mills. It also discusses the factors, including the design, operating parameters, and feed material The feed rate of Ball mill in the second plant is lower and it has a finer product. The highest P 80 values were obtained by grinding only in the rod mill for 10 min (step A). Ball mill(PDF) Processing of Magnetite Iron Ores–Comparing Grinding Options
احصل على السعر
Operational parameters affecting the vertical roller mill
A cement Vertical Roller Mill modeling based on the number of breakages. Vertical roller mills (VRM) are widely used to grind, dry, and select powders from various materials in the cement, electric power, metallurgical, chemical, and nonmetallic ore industries. For the sectors above, the VRM is a powerful and energy-intensive grinding A previous attempt at model-plant mismatch detection for a grinding mill, in the form of a partial cross correlation analysis, is used as a benchmark for model-plant mismatch detection and degraded sub-model isolation. This is followed by an investigation of the plant model ratio technique applied to the same system.Model-plant mismatch detection for a plant under Model
احصل على السعر
Grinding Mill Computer Model AusIMM
of the mill data base with only a limited number of variables considered. 3.2 Rod Mill Design A different approach is taken with the rod mill design where equations by Bond and Rowling are used to calculate the mill power draw. The Morgärdshammar equation and the IMM equations are shown for comparison. The method of use is similar Corn wet mills are relatively energy-, water-, and capital-intensive compared with other food processing industries. Each mill uses large amounts of water (1.5–1.78 L/kg or 10–12 gal/bu) in fractionating corn, which must be evaporated at considerable energy cost.Typical capital investments of $0.23–0.35/kg or 6–9/bu. of annual grinding capacity Wet Milling: The Basis for Corn Biorefineries ScienceDirect
احصل على السعر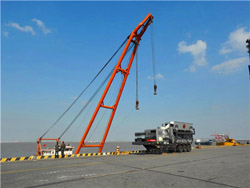
How to Choose the Right Grinding Mill for Mineral
You need to choose a grinding mill control that enhances the stability, efficiency, and reliability of the mill operation. Add your perspective Help others by sharing more (125 characters min.) Cancel
احصل على السعر- مصنع لإنتاج مسحوق السليكا الصور
- آلة مطحنة الكرة الرطب مطحنة الكرة
- kepanjangan ktc coal mining kaltim
- شرکت های تجهیزات معدن
- احدث المعدات الثقيلة 2013
- الكسارة الفكية الأولية للكسارة الأولية للمناجم
- graphite mine grinding falcon
- سعر آلة طحن الترموليت
- مطحنة خام الذهب جنوب أفريقيا
- آسیاب برای فرز منیزیم خط تولید
- ore crusher 200 mesh output
- معدات فصل مخلفات البناء
- مخروط محطم الدردشة على الانترنت
- مطاحن ختم الذهب للبيع في غانا
- gold mining ghana africa