اتصل
هاتف
+0086-371-86162511
عنوان
تشنغتشو ، الصين
ball grinding density

The kinetics and efficiency of batch ball grinding with
Since in industry grinding balls are generally made of steel-based alloys with a narrow density range of 7.50–8.20 g/cm 3, it is a usual practice to select larger-sized Since in industry grinding balls are generally made of steel-based alloys with a narrow density range of 7.50–8.20 g/cm 3, it is a usual practice to select larger-sized The kinetics and efficiency of batch ball grinding with
احصل على السعر
Measuring Density in Grinding Circuit Rhosonics
Measuring points. In the grinding circuit, possible installation points are in the ball mill discharge and feed (recirculation), (hydro) cyclone feed, overflow, and underflow. Example of a Rhosonics density meter (SDM), Cylpebs of equal diameter and length have 14.5% greater surface area than balls of the same mass, and 9% higher bulk density than steel balls, or 12% higher Comparison of grinding media—Cylpebs versus balls
احصل على السعر
(PDF) Grinding in Ball Mills: Modeling and Process
The paper presents an overview of the current methodology and practice in modeling and control of the grinding process in industrial ball mills. Basic kinetic and energy models of the grindingAccording to P-values, the final ranking of the significance of factors in grinding efficiency was as follows: pulp density > feed size > grinding time > ball diameter.Ball mill characteristics and test conditions
احصل على السعر
Minerals Free Full-Text The Effects of Ball-Mill Grinding
Although the effectiveness of grinding media (ball, rod, autogenous) has been shown for different materials, there are very few studies on the effect of the Cemented tungsten carbide balls (hereafter abbreviated as WC balls) are commonly applied in the grinding of wasted tool steel for purpose of reuse owing to their The kinetics and efficiency of batch ball grinding with
احصل على السعر
Minerals Free Full-Text Comparison of Particle
The diameter of the pin-type stirrer arm was 8.5 cm, and the number of stirrer arms was 5. Grinding tests were performed for each parameter at a constant grinding time. Alumina balls (spherical beads) Quartz (Lingshou County, Hebei Province, China) was used as the feed for the grinding test. The particle size distribution of the feed is illustrated in Fig. 1.The feed size was classified into three particle size classes: coarse size (class 1, +45 μm), desired size (class 2, −45 +10 μm), over-grinding size (class 3, −10 μm), and the percentage by Effect of grinding media properties and stirrer tip speed on
احصل على السعر
The effects of grinding media shape on breakage rate
Cylpebs of the same diameter and length have 50% greater surface area, and 45% greater weight, than balls of the same material. In addition, they have 9% higher bulk density than steel balls, and 12% higher than cast balls. The objective of this paper is to compare Cylpebs and ball grinding media in terms of grinding kinetics. 2. BackgroundBall grinding is considered as an effective method that transforms large particle powder into fine particles via high-speed rotation or vibration and generates a strong impact and grinding between the grinding ball and raw materials [14,15]. The vigorous collision and friction result in a pristine atomized surface on the powder particles [16,17Materials Free Full-Text Effect of Ball Milling Time on the
احصل على السعر
(PDF) Research on the Grinding Energy Density in a Jet Mill
Grinding is an important element in the processing of biological materials, such as cereal grains, woody biomass, food waste, etc., and its purpose is to reduce bulk density and storage areasThe two grinding media have different surface area, bulk density and contact mechanisms in grinding action. Comparative tests were conducted using the two types of grinding media in a laboratory Bond ball mill at various conditions of equality such as media mass, size distribution, surface area and input specific energy.Comparison of grinding media—Cylpebs versus balls
احصل على السعر
Temperature progression in a mixer ball mill Springer
The amount of heat that is dissipated is strongly dependent on the milling parameters that influence the energy input in the milling beaker. These parameters are the frequency ν osc, the milling ball diameter d MB, the milling ball filling degree Φ MB (Eq. 1), the milling beaker size, the grinding stock filling degree Φ GS (Eq. 2) and material Cylpebs of the same diameter and length have 14.5% larger surface area when compared to balls of the equal mass, and 9% higher bulk density when compared to steel balls, or 12% higher inComparison of Grinding Media-Cylpebs versus Balls
احصل على السعر
Studies in vibration milling ScienceDirect
This signifies that ball density Rate of grinding has considerable effect in grinding soft materials The equation for rate of grinding may O written as It has not been possible to correlate the data of the second region satisfactorily, due to the high ~ r' t s. values of slopes of plots in this region. There seems (9 Sue) = K2 Cap (W J S ) ~YHowever, the density of balls does affect the grinding efficiency. Show abstract. Cemented tungsten carbide balls (hereafter abbreviated as WC balls) are commonly applied in grinding of wasted tool steel for reuse owing to their extraordinary surface hardness (89.5 HRA) and high density (14.5 –14.9 g/cm 3). In this study, grinding Ball size distribution for the maximum production of a
احصل على السعر
The kinetics and efficiency of batch ball grinding with
TXX influence of changes in grinding media load and density on the grinding behaviour of trace quantities of quartz within an environment of calcite in a small continuous wet ball mill have beenMild steel balls and HCLA steel balls were used to examine the role that ball hardness play in grinding. Net production of −44-µm (−325-mesh) material reached maximum at 70% solids, whereas the ball wear decreased as pulp density increased. HCLA steel balls ground the taconite ore finer than mild steel balls under otherwise identicalEffects of percent solids and mill loading on ball wear in
احصل على السعر
An innovative approach for determining the grinding media
The dry grinding experiment was operated in the ball mill (Φ460 × 600 mm) with steel ball as grinding media at mill speed 47 r/min, space-filling factor φ 30%, and material ball ratio χ 0.6. The loading qualities of ore and steel ball were confirmed by eq. (5), (6). The loading quality of the steel ball was 145.5 kg, and the loading oreAbstract. In wet milling, the presence of a pool of slurry is generally the result of mill overfill. The effects of overfilling on milling kinetics have been examined. Assessment of milling efficiency has also been made. To this end, batch grinding tests were carried out at 75% of critical speed. A laboratory mill, filled with 20 mm balls, wasEffects of slurry pool volume on milling efficiency
احصل على السعر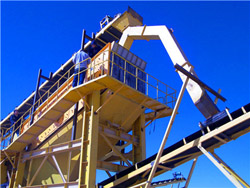
Ball Grinding Process SpringerLink
Ball grinding process is a grinding method of crushing ore with ball-shaped grinding medium in the grinding mill. In the ball grinding process, because the steel ball has 360° free rotation, it is suitable for falling motion and throwing motion. The ore slurry stored in the mill is less, and the minerals with high density are not easy toCeramic grinding, which in this paper is defined as a method of using ceramic materials as grinding media, is favored by many processing plants as an emerging high-efficiency and energy-saving grinding method. This paper investigates the effect of slurry mass concentration on the grinding characteristics of magnetite by taking the feed Effect of Slurry Concentration on the Ceramic Ball Grinding
احصل على السعر
Ball Mills 911 Metallurgist
CERAMIC LINED BALL MILL. Ball Mills can be supplied with either ceramic or rubber linings for wet or dry grinding, for continuous or batch type operation, in sizes from 15″ x 21″ to 8′ x 12′. High density ceramic linings of uniform hardness male possible thinner linings and greater and more effective grinding volume.There are three types of grinding media that are commonly used in ball mills: • steel and other metal balls; • metal cylindrical bodies called cylpebs; • ceramic balls with regular or high density. Steel and other metal balls are the most frequently used grinding media with sizes of the balls ranging from 10 to 150 mm in diameter [30].Grinding in Ball Mills: Modeling and Process Control
احصل على السعر
Grinding in Ball Mills: Modeling and Process Control
There are three types of grinding media that are commonly used in ball mills: • steel and other metal balls; • metal cylindrical bodies called cylpebs; • ceramic balls with regular or high density. Steel and other metal balls are the most frequently used grinding media with sizes of the balls ranging from 10 to 150 mm in diameter [30].Experience has shown that the best grinding conditions for ores in ball mills are created by a slurry density of between 70% and 80% solids by mass [15,16]. This implies that the milling rates are highest within this range. We investigated the effects of slurry density, grinding time and grinding energy on the grindability of a typical platinumSlurry density effects on ball milling in a laboratory ball mill
احصل على السعر- adv disadv of ball mill
- كيفية تصميم كسارة الفك الصغيرة
- آسیاب های استخراج طلا به تن در روز کلمبیا
- وضع مصنع طحن الكوارتز
- small lab ore gold mining machine
- میلز در مکزیک برای استخراج از معادن
- دستگاه های موبایل و سنگ شکن های صنعت سیمان
- كسارة متنقلة من جهة ثانية في الهند
- rock crushing plant process diagram
- كسارات حجر متحركة للبيع في استراليا
- كسارة vsi نظام الشحوم الاوتوماتيكي
- مستعملة ماكينات التعدين
- china crusher products crushing in bermuda
- خطرات ناشی از استخراج معادن سنگ گچ
- خطة كسارة متنقلة رسم تخطيطي