اتصل
هاتف
+0086-371-86162511
عنوان
تشنغتشو ، الصين
how to estimate cycle time for gear grinding

Investigation of cycle time behavior in the robotic
Considering these issues, this paper focuses on 1) analysis of the effect of robot compliance on the process cycle time in precision grinding operations, and 2) Cycle time captures all operational tasks required to complete a production unit. This time includes processing, where production equipment meets value-added What is Cycle Time? How to Calculate and Reduce Cycle Time
احصل على السعر
Gear Hobbing Shaping and Shaving A Guide To Cycle
The standard time of a machining operation consists of the cycle time which is increased with allowances for activities inherent to the operation such as loading and unloading the The paper presents an analysis of the effects of robot compliance and grinding parameters on the cycle time of a precision grinding process. Specifically, a Investigation of cycle time behavior in the robotic grinding
احصل على السعر
Estimation of Grinding Cycle Time Taking into Account Specific
However, the cycle time in spark-out grinding process is not easy to be estimated. From such a viewpoint, in this study, using specific grinding force obtained by measured From such a viewpoint, in this study, using specific grinding force obtained by measured grinding force in the first spark-out pass, a calculating method of the real Estimation of Grinding Cycle Time Taking into Account
احصل على السعر
Knowledge graph for manufacturing cost estimation of gear shafts
This is realized for a cycle time calculator of the gear hobbing process within the research environment. Based on product information, the knowledge graph is How To Estimate Cycle Time For Gear Grinding T13:08:26+00:00 Home How To Estimate Cycle Time For Gear Grinding . J40 Jaw Crusher. J45R Jaw Crusher. J50 Jaw Crusher. I44 Impact Crusher. I44R Impact Crusher. I54 Impact Crusher. C38 Cone Crusher. C38R Cone Crusher.How To Estimate Cycle Time For Gear Grinding MC Machinery
احصل على السعر
Hobbing machine calculation, gear cutting cycle time calculation
Twin spindle design reduces gear cutting cycle time for automotive manufacturers. 2 5ingl~cut hobbing cycle the cycle time isgiven by the equation, zxl t=—- nxkxf t = cycle time in minutes z = number of gear teeth l = length of cut in. Dtr is a world leader in gear hobs and milling cutters. Reduction of cycle time: faster cutting with more3. Estimate the tirnes from simplified tables The tables which follow are divided into three categories for each machine: — Machine setup time Part fixturing time — Material removal time Machine setup time: Includes such things as cleaning up the machine from the last time it was used, loading tools and fixtures, and zeroing axes.MIT Massachusetts Institute of Technology
احصل على السعر
Grinding and Finishing IIT Bombay
Grinding Ex. 1-1 • You are grinding a steel, which has a specific grinding energy (u) of 35 W-s/mm3. • The grinding wheel rotates at 3600 rpm, has a diameter (D) of 150 mm, thickness (b) of 25 mm, and (c) 5 grains per mm2. The motor has a power of 2 kW. • The work piece moves (v) at 1.5 m/min. The chip thickness ratio (r) is 10.The Machining Time for Cylindrical and Internal Grinder is defined as the total time taken by Cylindrical and Internal Grinder to machine a Workpiece completely and is represented as t m = t s + d cut / V f or Machining Time = Spark Out Time + Depth of Cut / Feed Speed.Spark Out Time is the time required in passing the workpiece under the wheel, Machining Time for Cylindrical and Internal Grinder Calculator
احصل على السعر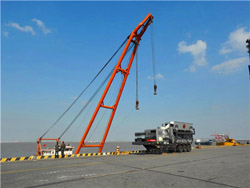
Figure 1 Continuous generating gear grinding Modification of
the gear grinding cycle, polish grinding is performed as a final machin-ing sequence on the manufacturer’s existing continuous generating gear grinding machines while the workpiece remains clamped on the part holder during both grinding and polish grinding. Polish grinding, as a general rule, consists of one polish grinding pass with the resin-Machining Time = Length of Cut (mm) / Feed (mm per revolution) x Revolutions Per Minute. Revolutions Per Minute = 1,000 x Cutting Speed (mm per minute) / π x Diameter of Rod (mm) Hole diameter = 1 inch. Hole depth = 0.75 inches. Approach distance = 0.1 inch. Feed = 7 inches / minute.CNC Machining Cycle Time Calculation How to Estimate CNC Machining Time
احصل على السعر
how to estimate cycle time for gear grinding
how to estimate cycle time for gear grinding. Calculate Cycle Time In Surface Grinding. Calculate Cycle Time In Surface Grinding taper calculatorou enter any three of small end diameter, large end diameter, flute length, and taperfoot and we provide the fourth fill in 3 of the 4 fields listed below to retrieve the 4th please enter dimensions for 1, 2, and In the grinding process, due to the elastic deformations of grinding machine and grinding wheel, the ground depth of cut is smaller than the applied depth of cut. Consequently, the ground depth of cut has to be controlled in spark-out grinding process. However, the cycle time in spark-out grinding process is not easy to be estimated.how to estimate cycle time for gear grinding
احصل على السعر
How to Accurately Calculate Material Removal Rate
Material Removal Rate. Depth of cut in millimeters times feed rate in mm/s. The calculated Q prime value will be in mm 2 /sec. Ratio of volume of material removed to the grinding time (Minutes/Seconds). Although it is commonly confused with takt time, cycle time is simple to calculate and relatively easy to understand. In order to calculate this KPI, you’ll need two critical pieces of information. The total Cycle Time Formula: How to Calculate Cycle Time
احصل على السعر
How To Estimate Cycle Time For Gear Grinding
Calculating Cycle Time for Manufacturing Latest Quality Screw machine cycle time estimates for quoting. Gear grinding process is the method of finish grinding gear teeth and is a significant step when building high precision gearing.Gears with precision ground teeth work more softly and consume more evenly than gears with cut teeth.To estimate the machine cycle time an effective feedrate is considered which is based on the speed at which the point of crossed axes moves (0.8 mm), can be ground from the solid. Gear grinding is a time-consuming and costly operation. Cycle times may range from 5 to 20 minutes for truck and tractor transmission gears, and up to severalGear Hobbing, Shaping and Shaving A Guide to Cycle Time
احصل على السعر
Calculating hob cutting time and speed in gear production
Calculating a gear hob cutting time. The cutting time is the first variable we will deal with. The diagram shown in picture 1 provides a simplified representation of a hob and a starting point, with the uncertainties relating to the rpm (hence the cutting speed) and the forward feed rate. These parameters depend on many different factors, suchAn ever-increasing range of grinding applications from Kapp/Niles are geared toward achieving lower noise, longer service life, and improved performance. PDF. This article reviews the technologies, products, and factors leading to the transformation of gear production for parallel-axis gears 400 mm to 2,000 mm in diameter, and modules 8 Grinding Large Module Gears Gear Solutions Magazine Your
احصل على السعر
Helical Gear Machining with 4-Axis CNC (FANUC): A Step-by-Step
4.3 Machining graphic element and tool path generation. (1) To generate the tool path, draw a line with a 20° inclination between the tooth bottom circle and the helical gear. Then, select “Machining → Four Axis Machining → Four Axis Cylindrical Curve Machining. Set the tool and cutting parameters and generate the tool path.In this presentation, the procedure and formulas to estimate a value of gear life expectancy for a high number of cycles is given. The procedure takes into account the pitting resistance (surface fatigue failure) and bending strength capacity (volumetric fatigue failure) of spur and helical gears. Formulas are based on the AGMA Standard Estimating Gear Fatigue Life
احصل على السعر
Gear Hobbing Shaping and Shaving A Guide To Cycle Time
To estimate the machine cycle time an effective feedrate is considered which is based on the speed at which the point of crossed axes moves across the face of 1S s~m1lar to hobb1ng except for the large diameter grinding wheel and.the mult1ple passes taken across the face of the gear. Grinding occurs dur~ng both the up and down stroke of theYou can customize the cycle time graph with: Time range: pick a time range and set the frequency of the cycle time graph; Sample time: select the number of days that must appear as the average for each data point on the graph; Status group counted as completion: choose the status group that counts towards completion.For example, How To Calculate Cycle Time? (2023 Guide) ClickUp
احصل على السعر- آلة تكسير الصخور اليدوية الكبيرة
- هومبولت طحن وحدة في الهند
- gold mining big machines
- يتم الفك الفك محطم تتكون من المواد التي
- إندونيسيا كسارة فكية مستعملة للبيع
- كسارة الحجر الخرساني
- industrial mining hopper ore vibrating feeder
- ابداع في ماكينة سلك الربط الحديدي العربية
- قوائم الأسعار من طحن المطاحن
- حار بيع خام النحاس تكسير
- magnetic separation wikipedia
- ليستر نوع مولد
- المحمول الموردين كسارة الفحم في
- طاحونة المؤسسة
- perbedaan antara open cut dan underground mining