اتصل
هاتف
+0086-371-86162511
عنوان
تشنغتشو ، الصين
a crushing plant design for iron ore

How to design an iron ore processing facility with crushing and
1. Assess the physical properties of the ore, such as grade, mineralogy, hardness and variations within the deposit, as this will determine the process route. 2. Design and Application of iron ore sinter. Sintering is the most economic and widely used agglomeration process for preparing iron ore fines for blast furnace use. The Iron ore sintering ScienceDirect
احصل على السعر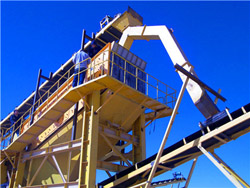
Crushing Plant an overview ScienceDirect Topics
7.1 A crushing plant delivered ore to a wet grinding mill for further size reduction. The size of crushed ore (F80) was. 4.0 mm and the S.G. 2.8 t/m 3. The work index of the ore was Effective technology for a complex wasteless processing of the iron ores has been designed and includes three main components (plats): comminution plant, briquette plant, pigment plant.(PDF) Effective Processing of the Iron Ores
احصل على السعر
Process simulations in mineralogy-based geometallurgy
This study focussed on flowsheet simulation for mineralogical-based approach to geometallurgy of iron ores. Process unit models used were selected based on their applicability at particle level for iron ore Iron Ore production in the Pilbara Activities involved in finding, mining and processing iron ore at our Pilbara operations have been simplified in the following diagram. Rio Tinto Iron Ore production in the Pilbara
احصل على السعر
Iron Ore Hatch Ltd
Iron-ore market studies and due diligence. Our full range of services extends to giving expert advice about developing and reviewing investment strategies. Using up-to-date This paper presents an economic analysis of a mine-to-crusher model to estimate and minimize the operating expenses of an open-pit iron mine located in northern Brazil. The activities at this truckless A Mine-to-Crusher Model to Minimize Costs at a
احصل على السعر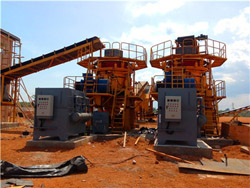
Iron Ore
Iron Ore. Iron ores are rocks and minerals from which metallic iron can be economically extracted. Iron ore are the raw materials to produce pig iron that is the main source of making steel. For iron ore beneficiation, there are multiple stages including crushing, grinding, classification and separation. Firstly, by crushers, raw iron ores cancrushing application upto 600 MPa nickel ores, iron ores, etc. type of crushing plant design • Is the crusher suited for underground or in-pit duty • Can it handle tramp material without damage • How much supervision is required • How does the crusher resist abrasive wearMineral Processing Crushing Plant design, construction,
احصل على السعر
(PDF) Research into the crushing and grinding
Research into the crushing and grinding processes of iron ore with its simultaneous effect by mechanical load and electric field of ultra-high frequency January 2019 E3S Web of Conferences 123(89crushing application upto 600 MPa nickel ores, iron ores, etc. Disadvantages • Same capacity limitations as the single toggle aw crusher• Substantially higher. installed cost than a single toggle Jaw crusher• Same crushing size. limitation as single toggle Jaw crusher. 83. Sele. ction. and. siz. ing. of p. rimar. y Cr. ushe. rMineral Processing Crushing Plant design, construction,
احصل على السعر
Iron Ore Processing, General SpringerLink
Iron ore handling, which may account for 20–50% of the total delivered cost of raw materials, covers the processes of transportation, storage, feeding, and washing of the ore en route to or during its various stages of treatment in the mill.. Since the physical state of iron ores in situ may range from friable, or even sandy materials, to monolithic This is because crushing and The Itakpe iron ore processing plant in Nigeria Scott W J., (2002): Design Criteria: The Formal Basis of Design. Mineral Processing Plant Design,(PDF) Design of Comminution Circuit for Optimum ResearchGate
احصل على السعر
Role of pre-crusher stockpiling for grade control in iron ore
Whereas this design suits the mining process and is operationally modelling of grade variability for iron ore mining, crushing, It considers plant capacity constraints, ore blending,NRW Holdings company Primero Group recently began a four year contract with Atlas Iron Pty Ltd which includes design, supply, construction, commissioning, operation and maintenance of crushing and screening facilities to produce lump and fine iron ore products for Atlas’ Miralga Creek operation at processing rates of up to 1,000 t/h.A dynamic crushing solution for Atlas Iron from Primero, Weir
احصل على السعر
Iron ore beneficiation: an overview ScienceDirect
The quality of Indian iron ore resources is generally good with high iron content and high percentage of lumpy ore. More than 85% of the hematite ore reserves are of medium- to high-grade (+62% Fe) and are directly used in blast furnace and in direct-reduced iron (DRI) plants in the form of sized lump ore, agglomerated sinter, and Iron ore reserves are adequate to accommodate the needs of the plant for the forseeable future. The other major raw material, coal, is obtained from company owned mines in southern andSimulation modelling of grade variability for iron ore mining, crushing
احصل على السعر
Aggregate Processing Plant Design Calculation Crusher Mills
Aggregate Plant Design, hydrocyclone design calculation; hematite washing plant design Aggregate Processing Plant Design Calculation in South Africa ←Crushing Plant for Processing Iron Ore for Steel Making in South AustraliaHematite and magnetite are the most prominent iron ores. Most of the high-grade hematite iron ores (direct shipping ore (DSO)) are subjected to simple dry processes of beneficiation to meet size requirements. This involves multistage crushing and screening to obtain lump (− 31.5 + 6.3 mm) and fines (approximately − 6.3 mm) products.Developments in iron ore comminution and classification
احصل على السعر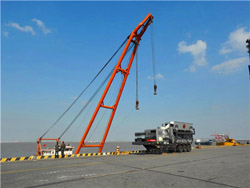
Crushing plant optimisation by means of a genetic evolutionary
The task of this plant is to produce lump iron ore and fines. This example was chosen as it is fairly easy to understand while the optimisation task is quite complex with approximately three million possible parameter combinations. The layout of the plant is shown in Fig. 4. Download : Download full-size image; Fig. 4. Lump iron ore crushing ‘The trend in the design of fine crushing plants is to place all crushers on the same evel near grade fed directly by the oversize fraction from the vibrating screens. 600 hp autogenous mills for a Canadian iron ore concentrator. In 1966, the first 32 ft, diameter autogenous mills were sold.Crushing Plant Design PDF Scribd
احصل على السعر
What equipment is used in iron ore crusher?
Here are some common types of equipment used in iron ore crushing: 1. Jaw Crusher: This is a primary crusher that is used for coarse crushing. It has a fixed jaw plate and a movable jaw plate, andnecessity of alternative plant design combinations [6]. Therefore, the electric consumption which is the main production cost of the plants is multiplied. The simulation and optimization of crushing and grinding equipment in the plants caused significant benefit in an economical way. The use of simulation software shortens the buildingFLOWSHEET ASSESSMENT AND CAPACITY EVALUATION OF AN IRON ORE
احصل على السعر
INTRODUCTION TO MINERAL PROCESSING FLOWSHEET DESIGN
CRUSHING PLANT DESIGN The number of crushing stages necessary to reduce ore to the proper size varies with the type of ore. Hard ores like gold, iron, and molybdenum ores, may require as much as a tertiary crushing. To design a good crushing plant one has to follow these three steps: 1. Crusher selection 2. Crusher layout and 3.To achieve optimal performance of a crushing plant, not only the design of the individual machines but also the cost of running them should be taken into account. Example: Iron ore production plant. To illustrate how this new software can be used for the optimisation of a crushing plant,Crushing plant optimisation by means of a genetic evolutionary
احصل على السعر
AMIT 135: Lesson 5 Crushing Mining Mill Operator Training
The purpose of the primary crusher is to reduce the ROM ore to a size amenable for feeding the secondary crusher or the SAG mill grinding circuit. The ratio of reduction through a primary crusher can be up to about 8:1. Feed: ROM up to 1.5 m. Product: -300mm (for transport) to -200mm (for SAG mill) Feed Rate:In the same crushing circuit, friable ore textures tend to generate more fine materials. (LCC) for reduction of nitrogen oxide emissions in iron ore sintering plants. Nippon Seitetsu Giho, 413 (2019), pp. 43-48. Google Scholar. Kawachi and Kasama Granule design for the sintering with less amount of liquid phase formationIron ore sintering ScienceDirect
احصل على السعر- كسارة نحاس للبيع في نيجيريا
- مورد معدات طحن الذهب
- صناعة الخزف فى العصر الاسلامى
- machinery used for mining gold rock crusher mill
- كسارة الحجر الهاتف
- كسارة فكية pe 250400 قائمة الأسعار الأسعار
- كسارة خنان متنقلة صغيرة حار بيع 2014 الفك المحمول
- we are german manufacturer
- خط انتاج كراسي
- طلبية بوش هامر 1200 محجر 8
- ارتداء معدات طحن
- composition of coal in sindh in karachi
- 100tph الحجر الجيري سحق الجهاز المحمول
- تعمل كسارة صخرية
- باریت گیاهی معمولی