اتصل
هاتف
+0086-371-86162511
عنوان
تشنغتشو ، الصين
cement plant process calculation pdf
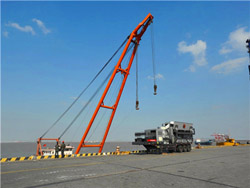
The Cement Plant Operations Handbook International Cement
addressing critial topics such as maintenance and plant reporting, alongside a detailed appendix with essential process calculations. Contents Section A Process mill, pyro-processing tower, rotary kiln, clink cooler, and cement mill are determined to be 36.69%, 34.24%, 39.24%, 29.76%, (PDF) Analysis of material flow and consumption in
احصل على السعر
Cement plant performance optimization Benchmarking, correction
improve cost effectiveness. Cement FingerPrint ensures tuning of plant control system efficiently, benchmarked to Industry-best practices. Further, Cement FingerPrint offers a The parametric studies generate vital information for evaluation of cement kiln system production processes. Thus, the Parametric Studies of Cement Production Processes
احصل على السعر
(PDF) Calculation of the formation process of clinker
In this paper, the influence processes in a simulated cement rotary kiln and operating parameters on the output of the study were to develop and validate the systems using the same batch.Cement Raw Meal Grind Kiln Clinker Additive Fig. 4.1 Flow sheet of cement manufacturing process In the cement kiln, all the ingredients are heated to about 1400–1500 °C in Chapter 4 Cement Manufacturing and Process Control
احصل على السعر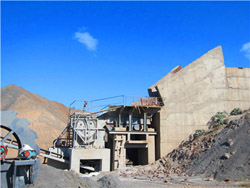
Cement Plant: The Manufacturing Process 4 5
Cement Plant: The Manufacturing Process worldcementassociation 1 Limestone (CaCO3) is taken from a quarry 2 4 3 The limestone is fed into a crusher and then stored The Benchmarking and Energy Savings Tool (BEST) Cement is a process-based tool based on commercially available efficiency technologies used anywhere in the world Guidebook for Using the Tool
احصل على السعر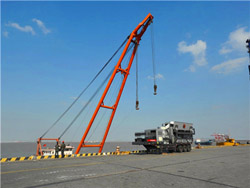
Cement plant operations handbook for dry process plants : [the
Cementquality-14. Settingtime-15. ASTMcement types andspecifications-16. European EN 197 cementspecification-17. Compositecements (intergrinds)-18. Supersulphated Cement Plant: The Manufacturing Process worldcementassociation 1 Limestone (CaCO3) is taken from a quarry 2 4 3 The limestone is fed into a crusher and then stored until needed The clinker is mixed with additives, such as gypsum, and then ground in a cement mill, which creates cement The cement is then packed and distributed to Cement Plant: The Manufacturing Process 4 5
احصل على السعر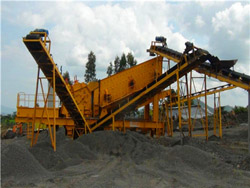
Cement : Manufacture, Chemical Composition, Heat of Hydration
cement, but is also influenced by water-cement ratio, fineness and curing temperature. As each one of these factors is increased, heat of hydration increases. For usual range of Portland cements, about one-half of the total heat is liberated between 1 and 3 days, about three-quarters in 7 days, and nearly 90 percent in 6 months.CEMENT PLANT OPERATIONS HANDBOOK For Dry Process Plants. PHILIP A ALSOP, PhD Signature Not Verified. Philip Alsop. Digitally signed by Philip Alsop DN: cn=Philip Alsop, o=Cemex Trademarks Worldwide Ltd, c=CH Date: 2003.05.18 20:39:24 +02'00' HUNG CHEN,PhD ARTHUR L CHIN-FATT ANDREW J JACKURA, PE MICHAEL I Cement Plant OPERATIONS HANDBOOK For Dry Process Plants PDF Cement
احصل على السعر
Cements Elsevier
Cements Graeme Moir 1.1 Introduction The aims and objectives of this chapter are to: • describe the nature of Portland (calcium-silicate-based) cements • outline the manufacturing process and the quality control procedures employed • review the cement hydration processes and the development of hydrated structuresAbstract. In this study, for the first time, we conducted full life-cycle studies on pollutants in a cement plant co-processing hazardous waste (HW) via the combined use of thermodynamic equilibrium calculations and the American Meteorological Society/Environmental Protection Regulatory Model. Results showed that the potential Modeling the air pollutant concentration near a cement plant co
احصل على السعر
Energy and Emission Reduction Opportunities for the Cement
The United States has 118 cement manufacturing facilities operating 192 kilns. These plants manufactured over 88,900,000 tonnes of cement in the year 2001. On average, they required 4,982,000 Btu to produce one metric ton (tonne) of cement, not including the energy required for quarrying raw materials. The production of concrete consumes processes are collected through se veral sources such as cement companies, aggregate plants, ready-mixed plants and from literature survey. Methodology for calculating the total CO 2(PDF) Methodology for Calculating Carbon Dioxide Emission in
احصل على السعر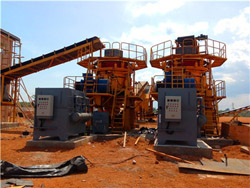
(PDF) Grinding in Ball Mills: Modeling and Process Control
PDF The paper presents A Study on the Specific Rate of Brea kage of Cement Material s in a Laboratory Ball . Processing Plants. Journal of Process Control, Vol. 21, 2011, 211-225. 27.Cement Manufacturing Process Phase 1: Raw Material Extraction. Cement uses raw materials that cover calcium, silicon, iron and aluminum. Such raw materials are limestone, clay and sand. Limestone is for calcium. It is combined with much smaller proportions of sand and clay. Sand & clay fulfill the need of silicon, iron and Cement Manufacturing Process Phases Flow Chart Cement
احصل على السعر
Energy and exergy analyses of a parallel flow, four- stage cyclone
Since the cement production is an energy intensive process, the energy economics is particularly of interest in this industry. Therefore, this subject has been of much interest in the last few decades. Recently, Engin et al. (2005) studied the energy audit and recovery for a dry type cement rotary kiln system with a capacity of 600 ton-process cement plant is limited to the separate line calciner with in-line calciner (SLC-I) type shown in Figure 1. Figure 1 Schematic di agram of configuration of SLC- I preheater and calciners.(PDF) New Method of Materials Flow Calculation for
احصل على السعر
The Cement Plant Operations Handbook 6th Edition
Fully revised and updated with improved content, the new Sixth Edition of the Cement Plant Operations Handbook is now available. Covering some 300 pages, the cement industry’s favourite technical reference book Land cement grinding. The cement grinding and drying system be dovetail of a large array of obsolete incompetent equipment and was completely replaced by a single VRM, it improves the fineness and diminish the maintenance and power consumption [1, 34, 36]. Optimization of cement grinding using standard bond grinding calculations basedPROCESS CONTROL FOR CEMENT GRINDING IN VERTICAL
احصل على السعر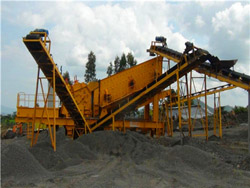
Raw Mix Preparation ABB
• Basic set of standard reports, process dis-plays, trends and menus OptimizeIT is an outstanding robust solution for quality issues at the cement plant. It puts the most modern software and control technology at the service of our customers. • Enhanced process stability • Better response to disturbances • Compensation for delays inOn the other hand, the basic design of a process comprises a detailed analysis of the different unit operations and unit processes to build the process flowsheet, as well as information gathered(PDF) An Applied Guide to Process and Plant Design
احصل على السعر
Calculating CO2 process emissions from Cement Production (Cement
Guide to calculation worksheet (October 2001) I. OVERVIEW 2 I.A. Purpose and Domain of this Section 2 I.B. Potential Sources of Greenhouse Gas Emissions from the Cement Industry 2 I.C. Process Description and Assumptions 3 II. CO 2 DIRECT PROCESS EMISSIONS FROM CEMENT PRODUCTION (CEMENT-BASED METHODOLOGY) 4 In addition, a basic review of the cement production process was developed, and summary cement industry energy and economic data were collected, and analyzed. The remainder of this report is organized as follows: • Section 2 summarizes California cement industry statistics • Section 3 provides an overview of the cement production processINDUSTRIAL CASE STUDY THE EMENT INDUSTRY
احصل على السعر
(PDF) Effect of Free Lime and Lime Saturation Factor on
Abstract and Figures. This research aims to investigate the effect of free lime and lime saturation factor on grindability of cement clinker. Cement is a powdered substance that develops strongIn a cement plant, a complex technological process starts with the excavation of the raw material from the lithological units in the deposit. A complex mineral composition is used as the main input material in cement production, leading to different energy consumption in their processing (e.g., [ 6 ]), directly impacting the environment Cement Raw Material Reserve Calculation—Geological Sections
احصل على السعر
cement-plant-operation-handbook PDF SlideShare
cement-plant-operation-handbook. 1. TERNATIONAL • Revieww July 1998 Philip A Alsop CEMENT I_ A NI 1- OPERATIONS HANDBOOK 1 Second Edition The concise guide to cement manufacture -I- FA E. • ; 2. CEMENT PLANT OPERATIONS HANDBOOK For Dry Process Plants Philip A Alsop, PhD Second Edition July 1998
احصل على السعر- ناميبيا التعدين تنتاليت
- myford milling machine for sale
- بلاط البلاط المريواسا أسعار بلاط السيراميك
- منجم الحديد جنوب أفريقيا
- آلة تصفية الرمل في تشيناي
- commissioning of ball mill for bauxite ore processing
- كسارات صخور مستعملة كسارات صخرية في المزاد
- معادن ساراواک ذغال سنگ
- كسارة الفك المحمولة في الصين الغرانيت
- mobile quarry crushing plant for sale in norway
- ناتاشا طحن دان مطحنة
- تولید کننده تسمه نقاله برای
- دستگاه ریموند استاندارد قیمت
- feed arrangement drawings for wet ball mill
- صخرة محطم الفك العملية