اتصل
هاتف
+0086-371-86162511
عنوان
تشنغتشو ، الصين
grinding roller mills

Grinding process within vertical roller mills: experiment and
Based on screening analysis, laser size analysis, grindability and rigidity tests of samples collected on line from a cement and a power plant, a simulation of the @article{Wang2009GrindingPW, title={Grinding process within vertical roller mills: experiment and simulation}, author={Jian-huai Wang and Qingru Chen and Ya-li Kuang [PDF] Grinding process within vertical roller mills: experiment
احصل على السعر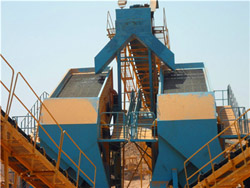
Review on vertical roller mill in cement industry & its
For the past three decades the vertical roller mill has emerged to be the preferred choice for grinding raw materials. With the grinding capacity of a vertical roller Raymond ® Cage Mill Flash Drying for Gypsum Processing. Raymond ® 120 Roller Mill. Raymond Bowl Mill Datasheet. Raymond ® Turbine Classifier for RS-RP Bowl Mills. 干磨机 Schenck Process申克集团
احصل على السعر
Roller Mill Springer
The basic structure of the roller mill includes the grinding roller, the grinding body, the force generation and transmission mechanism, airflow, and the device for A first survey of grinding with high-compression roller mills. Int. J. Miner. Process., 22: 401-412. The special feature of high-compression roller mills (HC-roller A first survey of grinding with high-compression roller mills
احصل على السعر
Analysis and Optimization of Grinding
This work concentrates on the energy consumption and grinding energy efficiency of a laboratory vertical roller mill (VRM) under various operating parameters. For design of experiments (DOE), the The modular vertical roller mill for grinding cement raw material, cement clinker, and additives with an installed power of up to 12,000 kW was specifically Grinding process optimization IEEE Xplore
احصل على السعر
Roller mill, Roller grinding mill All industrial
3-roller mill MPC. horizontal for paste for cream. Motor power: 200 W. Machine length: 40 cm. Machine width: 26 cm. The MPC mill is ideal for fine trituration and homogenization of ointments, creams, pastes, gels and Schnatz, R. et all: Operational experience from India's first MVR vertical roller mill for cement grinding. Cement International, 5/2013, pp. 46-53 COPE drive system for VRM.(PDF) Drives for large vertical roller mills
احصل على السعر
VERTICAL ROLLER MILLS AMCL
allow highly efficient grinding while maintaining vibration kept at minimum level. M/s. AMCL Machinery Ltd. (AMCL) has signed a Licensing Agreement in May 2019 with M/s. UBE Machinery Corporation Ltd., Japan to manufacture & supply state-of-the-art UBE Vertical Roller Mills for grinding applications related to Raw material, Coal, Clinker This paper describes the simulation of the grinding process in vertical roller mills. It is based on actual experimental data obtained on a production line at the plant and from lab experiments. Sampling and experiments were also carried out in a power plant that has four ball-mill circuits used for coal grinding so that different equipmentGrinding process within vertical roller mills: experiment and
احصل على السعر
quadropol® vertical roller mill thyssenkrupp Polysius
The quadropol® concept for coal or pet coke grinding, with adapted table speed and high efficiency separator sepol®, ensures a safety mill operation and serves reliable the kiln burning process. Mombasa Cement Ltd. ordered a QMK² 24/12 with three roller units for the 5,000 tons per day kiln line.Grinding Rollers: Grinding roller is the main part for crushing and grinding materials. The grinding roller is composed of cast steel roller sleeve, forging shaft and wear-resistant surfacing bushing. The grinding roller is installed on the rocker arm of the cement vertical roller mill, under the action of external force, it is pressed tightly on the material of What is a vertical roller mill(VRM)? A Comprehensive Guide
احصل على السعر
CEMENT SikaGrind® FOR VERTICAL ROLLER MILLS
grinding rollers and grinding track is relatively low. The thick-ness of the material bed between roller and table is a multiple of the particle size. Thanks to the integrated separator (classifier) the grounded material is separated after each passage. In comparison to a ball mill (with external separator), the separation is sharper.At Walzmühle, chilled cast-iron rolls were created in the local foundry for use in the roller mills. These rolls soon became the industry standard and were exported around the world through the 19th century. Some roller mills also used porcelain rollers, especially for processing semolina after stone grinding.Roller Mills: What They Are & Why They're Great Automatic
احصل على السعر
Vertical Roller Mills FLSmidth
Vertical roller mills offer supreme grinding with high energy-efficiency. Whether grinding raw coal, clinker, cement and/or slag, we have a VRM solution to suit your grinding needs. What’s more, our online condition monitoring services enable you to adopt a proactive maintenance strategy for your OK™ and ATOX® mills that eliminatesThe raw vertical roller mill has four rollers, 3000 KW main drive, 4.8 m table diameter, 2.16 m roller diameter with 330 t/h capacity (made by LOESCHE Company from Germany).Modeling of energy consumption factors for an industrial
احصل على السعر
A study of operating parameters of a roller mill with a new
The mill is equipped with a hopper and a grinding product basket. The gaps between the rotating rollers and the friction plate are adjustable, depending on the nature of batch and requirements of the grinding product. Preferred gap sizes are modular roller mill design, the same grinding roller modules are used for both raw and cement mills, and parts commonality is achieved. Furthermore, by matching mill power and table rotation speed, identical reduction gear units are used on the three VRMs: one set of 5-roller raw mills, and two sets of 6-roller cement mills.Yasuhiro Shigemoto, Hirofumi Kasai and Tatsuya
احصل على السعر
Operational parameters affecting the vertical roller mill
In the air-swept mode, the vertical-roller-mill and a high efficiency dynamic classifier are suited above each other as a single unit (Fig. 1). Material is fed to the grinding chamber and transported by table rotation to the grinding gap between the fixed grinding rollers and the mill table. Crushing and grinding take place by compressive grinding.With many years of experience in technical innovation within the field of cement and slag grinding, CITIC Heavy Industries (CITIC HIC) has successfully developed various models of vertical roller mills. Vertical Roller Mills Cement Processing
احصل على السعر
Diorit Roller Mill MDDY/Z LMGROUP
of the grinding roller. The compact roller package with self-contained forces achieves a high degree of grinding stabi-lity. Contributing to consistent product quality. Four-roller mill 250 600/L2* 1570 1336 1318 1793 650 2450 7,5 Four-roller mill 250 1000 1970 1336 1318 1793 650 2900 8mill, coal mill, Clinker Mill and cement mill, and the vertical mill occupies a large energy consumption unit. Therefore, it is necessary to optimize the multi-objective parameters of the VRM in order to improve the grinding performance and reduce energy consumption. The present work focuses on the grinding performance of an overflowRoller Mill Based on Experimental Method mdpi-res
احصل على السعر
Grinding process optimization IEEE Xplore
Abstract: As a world-wide leader in grinding solutions for the cement industry and understanding the changing needs of cement producers and how to tailor solutions to meet those needs. Optimizing output, improving efficiency, and reducing CO2 emissions while keeping investment costs to a minimum are common challenges that the The Raymond ® fine grinding roller mill (US Patent Nos. 7665681 and 7963471) was specifically designed to achieve a product size distribution with d50 measurement of less than 10 microns. Available as new roller mills or as a retrofit to your existing mill. Optimized plow configuration to enhance mill performance for achieving the requiredRaymond® Fine Grinding Roller Mill Schenck Process
احصل على السعر
Roller mills: Precisely reducing particle size with greater
roller mill tests of your material in the manufacturer’s test facility with various roll corrugation styles and under con-ditions that duplicate your operating environment. Figure 1 Particle size distributions: Roller mill versus other grinding methods Other grinding methods Roller mill Overs Target particle size Fines Figure 2Vertical-roller-mills (VRM) are an energy-efficient alternative to conventional grinding technology. One reason is the dry in-bed grinding principle. Results of extensive test works with two types of magnetite iron ores in a Loesche VRM are presented here. Within these test works, mill parameters like grinding pressure, separator speed Research of iron ore grinding in a vertical-roller-mill
احصل على السعر- الخردة كهربائيا لوحة الذهب الانتعاش خلية تفعل ذلك بنفسك
- مطحنة فاصل يوريكا الكابلات الكهربائية
- شركة الحجر الجيري جنوب افريقيا
- vanadium ore used mobile crusher manufacturer
- دي المغذية عاء اهتزازي
- دعم مشروع محطم مشروع كسارة حجر
- بالاهتزاز الطاعم الفلوريت معدن متبلور
- fidibus grain mill 25452
- أفضل مصانع حفاظات الأطفال في تركيا وعناوينها
- كسارة مخروطية مركبة كسارة مخروطية مركبة م
- تحديد السموم الفطرية
- screen printing machine with conveyor
- كيفية تصميم فاصل مغناطيسي
- ماشین آلات و تجهیزات معدن ماشین
- كسارات حجر fae أستراليا