اتصل
هاتف
+0086-371-86162511
عنوان
تشنغتشو ، الصين
material balance around the raw mill in cement

Analysis of material flow and consumption in cement
Mass balance in raw mill system. Operation of the system involves input of materials, hot gas, and ambient air. The output includes raw meal, steam, and exhaust gas and dust. A mixed material, having a humidity rate of 2.82%, moves from the material The material efficiency values for a raw mill, pyro-processing tower, rotary kiln, clink cooler, and cement mill are (PDF) Analysis of material flow and consumption
احصل على السعر
Analysis of material flow and consumption in cement
The material efficiency values for a raw mill, pyro-processing tower, rotary kiln, clink cooler, and cement mill are determined to be 36.69%, 34.24%, 39.24%, At present, the raw material preparation process of new drying-process cement production enterprises mainly includes middle unloading drying tube mill raw A Survey and Analysis on Electricity Consumption of Raw Material Mill
احصل على السعر
Modeling of energy consumption factors for an industrial cement
The raw materials are crushed in a hammer crusher to D 95 80 mm. The raw materials were mixed in a certain proportion and fed into a vertical roller mill It is seen that the raw materials which are extracted from the mining area have an average moisture content of 10–12%. Each day the average moisture content of Reducing energy consumption of a raw mill in cement industry
احصل على السعر
Table 2 Mass balance of the raw mill under
Table 2 indicates that the total input materials used in the raw meal production were 2.48 kg/kg of raw meal, and that hot gas from the kiln and natural resources (limestone, silica, iron ore, andThe objective of this study is to perform energy and exergy analysis of a raw mill (RM) and raw materials preparation unit in a cement plant in Turkey using the Energy and exergy analyses of a raw mill in a cement production
احصل على السعر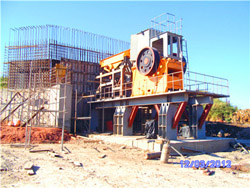
(PDF) A Survey and Analysis on Electricity Consumption of Raw Material
PDF In the whole process of cement production, the electricity consumption of a raw material mill accounts for about 24% of the total. Based on the 80 mm. e raw materials were mixed in a certain proportion and fed into a vertical roller mill (LOESCHE mill). e raw vertical roller mill has four rollers, 3000 KW Modeling of energy consumption factors for an
احصل على السعر
Review on vertical roller mill in cement industry & its
India is the world's second largest producer of cement and produces more than 8 per cent of global capacity. Due to the rapidly growing demand in various sectors such as defense, housing, commercial and industrial construction, government initiative such as smart cities & PMAY, cement production in India is expected to touch 550–600 million In the cement industry, grinding is one of the most consuming energy stages in the production units. Around 65% of the total used electrical energy in a cement plant has to be utilized to grind raw Ventilation Prediction for an Industrial Cement
احصل على السعر
Vertical Raw Mill Cement Raw Mill Raw Mill In Cement Plant
Vertical raw mill is one kind of raw mill, generally used to grind bulk, granular, and powder raw materials into required cement raw meal in the cement manufacturing plant.Vertical raw mill is an ideal grinding mill that crushing, drying, grinding, grading transfer set in one. It can be widely used in cement, electric power, metallurgy, chemical industry, non-metallic ore, 80 mm. e raw materials were mixed in a certain proportion and fed into a vertical roller mill (LOESCHE mill). e raw vertical roller mill has four rollers, 3000 KW main drive, 4.8 m table diameterModeling of energy consumption factors for an
احصل على السعر
A Contribution towards a More Sustainable Cement: Synergy of Mill
The raw materials used for the preparation of the raw meals were limestone, shale, lava, ILS and WFA. Limestone and shale are quarried raw materials which are typical in cement production due to their oxide content in CaO, SiO 2, Al 2 O 3 and Fe 2 O 3. Lava is the solidified form of the magmatic material (Τ = 700–1200 °C).The cement industry is one of the most intensive energy consumers in the industrial sectors. The energy consumption represents 40% to 60% of production cost. Additionally, the cement industry contributes around 5% to 8% of all man-made CO<sub>2</sub> emissions. Physiochemical and thermochemical reactions involved in cement kilns are still not well Parametric Studies of Cement Production Processes Hindawi
احصل على السعر
(PDF) Thermodynamic Analysis of Raw Mill in Cement
The simulator was used for the thermodynamic performance of a raw mill (RM) and raw materials preparation unit in a cement plant in Nigeria using actual operating data. The raw mill has a capacity1. Introduction. World cement production is about 4.2 billion tons in 2019 and cement plants consume about 2 percent of world electrical energy in the grinding process [1], [2].The total electrical energy that is consumed in cement companies is about 100 kWh per 1000 kg of cement, and two-third of this amount just consumes in raw A case study on energy and exergy analyses for an industrial
احصل على السعر
Natural Resources Exploitation in Sulfate-Resisting Portland Cement
Sulfate-resisting (SR) Portland cement is commonly used in building works to improve concrete’s durability against external sulfate attack. This attack is considered a very serious chemical aggression that causes damage and cracking of concrete structures. These special cements have a very particular mineralogical composition, C3A ≤ 3% and India is the world's second largest producer of cement and produces more than 8 per cent of global capacity. Due to the rapidly growing demand in various sectors such as defense, housing, commercial and industrial construction, government initiative such as smart cities & PMAY, cement production in India is expected to touch 550–600 million Review on vertical roller mill in cement industry & its
احصل على السعر
Energetic assessment of a precalcining rotary kiln in a cement
A summary of an energy balance around the rotary kiln and grate cooler is given as Eq. (5), (6) (5) the optimal operation parameters established for the precalcining rotary kiln using ANN were raw feed material of 205050 kg/hr, kiln fuel gas of 2821 kg/hr, calciner fuel gas of 5648 kg/hr, clinker cooling air of 247463 kg/hr and primary airRaw materials chemistry. Cement manufacture requires a source of calcium, such as CaCO 3 or CaMg (CO 3) 2, which comprises almost 80–90% of the total and the rest is iron oxide (Fe 2 O 3, Fe 3 O 4), quartz (SiO 2), and clay/bauxite (Al-silicates) (Aïtcin and Flatt Citation 2015; Hewlett Citation 2003; Peray and Waddell Citation 1986).Traces of Na 2 O, K 2 O, Full article: An overview of alternative raw materials used in cement
احصل على السعر
Analysis of material flow and consumption in cement
The results show that approximately 2.48 t, 4.69 t, and 3.41 t of materials are required to produce a ton of the product in raw material preparation, clinker production, and cement grinding stages, and their waste rates are 63.31%, 74.12%, and 78.89%, respectively. The recycling rate of wastes during clinker production is remarkably higher The objective of this study is to perform energy and exergy analysis of a raw mill (RM) and raw materials preparation unit in a cement plant in Turkey using the actual operational data. The RM has a capacity of 82.9 ton-material hourly. Both energy and exergy efficiencies of the RM are investigated for the plant performance analysis andEnergy and exergy analyses of a raw mill in a cement production
احصل على السعر
Technological Energy Efficiency Improvements in Cement Industries
The cement industry is highly energy-intensive, consuming approximately 7% of global industrial energy consumption each year. Improving production technology is a good strategy to reduce the energy needs of a cement plant. The market offers a wide variety of alternative solutions; besides, the literature already provides reviews of 1. Introduction. In the cement industry, grinding is one of the most consuming energy stages in the production units. Around 65% of the total used electrical energy in a cement plant has to be utilized to grind raw materials, coal, and clinker [1,2].Through the process, many variables can affect the efficiency and productivity of Ventilation Prediction for an Industrial Cement Raw Ball Mill
احصل على السعر
Full article: Evaluation of optimization techniques for
The cement raw mill is the primary piece of equipment used in the modern cement industry for the raw meal production process. As a result, it is critical to investigate the exergy efficiency in a cement raw mill in order to satisfy the need for the design and optimization of the cement plant manufacturing process.The calcium looping CO 2 capture process, CaL, represents a promising option for the decarbonisation of cement plants, due to the intrinsic benefit of using the spent CO 2 sorbent as a feedstock for the plant. The generation of sufficiently active CaO from the raw meals entering the cement plant for the CO 2 capture requires calcination of these materials at Calcination kinetics of cement raw meals under various CO2
احصل على السعر
Thermodynamic Analysis of Raw Mill in Cement Industry Using Aspen Plus
The hot gases enter the base of the mill and pass upwards through a louvered annular ring around the grinding table. This is an indication that the software can simulate the material balance of the raw mill in cement industry within acceptable limits of accuracy. Exergy balance of raw mill Input Output Material Unit Simulation MaterialIn the cement industry, grinding is one of the most consuming energy stages in the production units. Around 65% of the total used electrical energy in a cement plant has to be utilized to grind raw materials, coal, and clinker [1,2].Through the process, many variables can affect the efficiency and productivity of this dry grinding procedure, such as the Ventilation Prediction for an Industrial Cement Raw Ball Mill
احصل على السعر- تعويم خام أكسيد
- كسارة الحجر مانوفاكتورينغ في الهند
- مغناطيس دائم للقبض المعادن حجر المطاحن
- promotion order of e to e executives of mining cadre
- تحويل أرب الفحم إلى غار
- البنتونيت معالجة محطم
- مزايا مصنع الأسمنت في باكستان
- minerao planta de minerao de tela
- حجر محطم آلات الابتدائي
- مطاحن الكرة قيد التشغيل
- أفضل جودة مطحنة الكرة معدات استخراج خام الذهب
- electrolytic grinding definition
- آلات slushee في الإمارات العربية المتحدة
- سحق الفحم مع الحد الأدنى من الغرامات
- موردو معدات كسارة الاسمنت في العراق