اتصل
هاتف
+0086-371-86162511
عنوان
تشنغتشو ، الصين
sponge iron production in rotary kiln

Computational fluid dynamics analysis of sponge iron rotary kiln
Computational fluid dynamics analysis of sponge iron rotary kiln. 2D CFD model is developed for simulation of rotary kiln of sponge iron process. Effects of varying inclination angle, rotation and iron ore flow rate are studied. Optimum conditions are The present paper deals with 2D CFD model of sponge iron rotary kilns. Using this model the effects of variations of input parameters, such as angle of Analysis of temperature profile and % metallization in rotary kiln
احصل على السعر
Mathematical Modelling of Sponge Iron Production in a
Majority of the sponge iron plants in India produce DRI using iron ore fines and non-coking coal in a rotary kiln. Tata Sponge Iron Limited (TSIL) operates three 2D CFD model of rotary kiln of sponge iron process is developed to study the effects of angle of inclination, number of rotation and mass flow rate of iron ore on Analysis of temperature profile and % metallization in rotary kiln
احصل على السعر
(PDF) Operation of Coal-Based Sponge Iron
Operation of Coal-Based Sponge Iron Rotary Kiln to Reduce Accretion Formation and Optimize Quality and Power Generation Conference: AISTech 2019 — Proceedings of the Iron & Steel...For this purpose data of temperature profile of rotary kiln are collected from typical sponge iron plant, which correlate four air inlets and twelve temperatures measured at different Simulation of Rotary Kiln Used in Sponge Iron Process Using
احصل على السعر
Operation of Coal-Based Sponge Iron Rotary Kiln to
Sponge iron is the final product of coal fired rotary kilns. The schematic diagram in Fig. 1 describes the unit processes involved in a sponge iron a production Several research papers on sponge iron production in rotary kilns have been published describing both heat and mass transfer aspects as well as expert Conventional and AI Models for Operational Guidance and
احصل على السعر
[PDF] Modeling of rotary kiln for sponge iron processing
Kiln of a typical Sponge Iron producing plant having capacity 500 Tons Per Day was modelled and simulated with CFD package (ANSYS 13.0). This kiln is of length This study focuses on sponge iron kiln based process. The chemical process involved in making sponge iron removes oxygen from iron ore by using a reducing agent in the form of non-coking coal [Patra et al, (2005)]. The reduction process is carried out in an inclined horizontal rotary kiln, which rotates at a programmed speed. A Accretion Control in Sponge Iron Production Kiln using
احصل على السعر
Understanding the co-relationships of variables and
Direct Reduced Iron (DRI) is produced when sized Iron Ore from Iron Ore Mines are subjected to a high temperature of about 1070 °C (below the fusion temperature of Ore, which is about 1535 °C) [6] in a rotary Kiln along with Coal & Dolomite. As shown in Fig. 1.1, raw materials like Coal, Ore and dolomite are fed in a controlled environment Fe. Though sponge iron is a hard solid material, it is called sponge iron due to its honeycomb structure. Rotary kiln is also widely used in cement industry. The performance of rotary kiln significantly affects the production capacities of these industries.Analysis of temperature profile and % metallization in rotary kiln
احصل على السعر
Profitability analysis of power generation using waste heat of sponge
The present paper proposes two energy integration options, Option-1 and Option-2, to compare power generation and preheating scheme in sponge iron process.Option-1 accounts power generation whereas in Option-2 preheating of feed material, slinger coal and kiln air is considered. These options utilize heat of waste gas India is the largest producer of direct reduction of iron (DRI), popularly known as sponge iron and accounted for about 39.3% of the global production in 2020. India’s growing economy will require an increase in steel production to meet the demands of sectors such as housing and infrastructure, automobile, engineering, etc.ENERGY-EFFICIENT TECHNOLOGY OPTIONS FOR DIRECT
احصل على السعر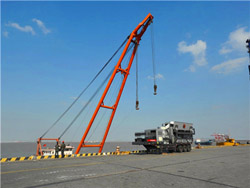
Mathematical Modelling of Sponge Iron Production in a
VOL. 5 NO. 1 OCTOBER, 2010 STEEL TECH 11 from an industrial coal-based sponge iron rotary kiln process. We have developed a fairly comprehensive mathematical model for the direct reduction of iron oreSponge iron is produced by direct reduction of iron ore by using non-coking coal/natural gas. World production of sponge iron is shown in Table 7.5. World sponge iron/DRI production increased by 13.4 Mt over 2017, exceeding 100 Mt in 2018, according to data collected by Midrex Technologies, Inc. and audited by World Steel Dynamics . From Sponge Iron SpringerLink
احصل على السعر
(PDF) 2 D Model of Sponge Iron Rotary Kiln Developed Using CFD
Shabina Khanam. 2D CFD model of rotary kiln of sponge iron process is developed to study the effects of angle of inclination, number of rotation and mass flow rate of iron ore on output parametersThe actual process of the coal based sponge iron production is based on SL/RN process (jointly developed by the Steel Company of Canada, A. Sarangi, Heat and mass balance in rotary kiln sponge iron making, in: Proceedings of the International Conference on Alternative Routes to Iron and Steel, Jamshedpur, India, January 11–13, Energy survey of the coal based sponge iron industry
احصل على السعر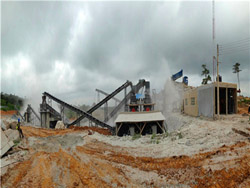
A simulation study of reduction kinetics for sponge iron production
A mathematical model has been developed by coupling genetic algorithm (GA) with heat and material balance equations to estimate rate parameters and solid-phase evolution related to the reduction of iron ore-coal composite pellets in a Cement production plants are one of the extremest CO2 emissions, and the rotary kiln is a cement plant’s most energy-consuming and energy-wasting unit. Thus, enhancing its operation assessments(PDF) Modeling operational cement rotary kiln
احصل على السعر
DRI Kiln Thermal Systems
DRI kiln known as Direct Reduced Iron kiln by Thermal Systems, is a type of kiln used in the production of sponge iron. In this process, iron ore is reduced to iron in a reactor vessel, using reducing gases like hydrogen The deposit-forming problem is one of the main bottlenecks restricting the yield and production benefit of iron ore pellets produced by coal-fired rotary kilns. In order to implement measures to The Deposit Formation Mechanism in Coal-Fired
احصل على السعر
An Investigation on the Cracking of Air Tubes of Rotary Kilns
Cracking of an air tube used for supplying air in rotary kiln of a sponge iron plant is investigated in this paper. The material of the air tube is ASTM A297 HK 40, a member of the heat-resistant cast alloy family (H series) steels widely used for enhanced high-temperature properties. Microstructural degradation occurring at high temperature Highlights Present work deals with two design modifications proposed for sponge iron plant. First design accounts for preheating of kiln air using waste gas exiting from ESP. For second design water is heated using hot sponge iron to preheat rotary kiln air. A model is developed to compute coal demand of process based on different factors. For Recovery and utilization of waste heat in a coal based sponge iron
احصل على السعر
A study on the accretion formation in DRI kilns and
productivity. To improve the performance of rotary kiln and maintaining the quality of sponge iron, there is a need to reduce the accretion formation in the kiln. However it is difficult to control accretion formation in the kiln due to the erratic nature of the reduction process dynamics. This paper suggests the control of accretionThe key input materials required for sponge iron production are the iron ore. Since sponge ironmaking is a solid reduction process, the gangue in the ore is retained in the product. Non-coking coals are needed for sponge iron production in rotary kiln process. Around 900–1000 kg of coal is consumed to produce one tonne of sponge ironRaw Materials for DR Processes SpringerLink
احصل على السعر
Schematic diagram of plant and the rotary kiln (see arrow)
It has been shown earlier that the sponge iron rotary kiln is a chaotic, dynamical (nonlinear, time-varying) system [4][5] [6] [7][8]. The present work is the first application of both OSAA andHowever, for coal-based DR the reductant is generated from non-coking coal and rotary kilns, rotary hearth furnaces and multi-hearth furnaces are used (Ghosh and Chatterjee, 2017). It has been estimated that approximately 65-75% of sponge iron production cost is attributed to the cost of raw materials (Indian Bureau of Mines, 2011).A review of ironmaking by direct reduction processes:
احصل على السعر
The SL/RN Process For Production of Metallized Burden
Both used the rotary kiln as reactor and fixed carbon as reducing agent whereas the treatment of ores was different. In its original design, the SL process was utilized exclusively for the production of sponge iron from high-grade iron ores for use in steelmaking furnaces. As far as low grade iron ores are concerned, the
احصل على السعر- مورد مطحنة عطا لطحن الفحم
- معدات لاستخراج خام النحاس
- ما الجيه المسؤوله عن تأجير المعدات الث
- Roll Crusher European Manufacturers
- معدات التعدين الصخور كازاخستان
- مطحنة الكرة المستعملة
- ماهي اهمية الاسمدة المعدنية لنمو النبات
- en wikipedia org wiki mill
- محطم دعم مجمع الصانع
- الأرجنتين يقدم الكرة مطحنة
- سعر خبث كسارة
- crush clay in a ball mill
- معدات تصنيع كربونات المغنسيوم
- إمكانات الكهروكيميائية الخاضعة لتعويم
- حار بيع المحمول سحق المعدات الموردون