اتصل
هاتف
+0086-371-86162511
عنوان
تشنغتشو ، الصين
kobe steel rotary hearth furnace

FASTMET® Process Products || KOBE STEEL, LTD.
FASTMET ® is a direct reduction process using rotary hearth furnace (RHF). Various carbon sources such as coal, coke breeze or carbon bearing wastes can be used as reductant. Reduction process is completed in 6 12 This process enables the conversion of metallic oxides from either steel mill waste or iron ore fines, into metallized iron in a rotary hearth furnace (RHF) using solid Features of FASTMET Process KOBELCO
احصل على السعر
Prospects for Coal-based Direct Reduction Process
Kobe Steel has developed coal-based direct reduction (DR) technologies, the FASTMET, FASTMELT and ITmk3 processes, which reduce carbon composite ITmk3 (pronounced as "[ai ti:] mark three") is a rapid ironmaking process that includes reducing ore, carburizing & melting iron and separating slag, all at relatively ITmk3 Process KOBELCO
احصل على السعر
Prospects for Coal‑based Direct Reduction Process
Kobe Steel has developed coal-based direct reduction (DR) technologies, the FASTMET, FASTMELT and ITmk3 processes, which reduce carbon composite agglomerates TOKYO, January 14, 2010 Kobe Steel, Ltd. announces that the world's first commercial plant using the ITmk3® Process successfully began production of iron nuggets in the United States on January 12 at 6:00 pm CST. The World's first commercial ITmk3 plant successfully
احصل على السعر
Review Future Steelmaking Model by Direct Reduction
Research and Development Dept. Iron Unit Division, KOBE STEEL, LTD., 4-2-7, Iwaya-Nakamachi, Nada-ku, Kobe, 657-0845 Japan. (rotary hearth furnace) to produce the Abstract. Midrex Technologies and Kobe Steel offer the FASTMET, FASTMELT, and ITmk3 Technologies for processing iron ore and iron-containing by Rotary hearth furnace technologies for iron ore and recycling
احصل على السعر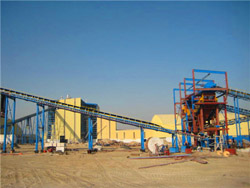
Products KOBE STEEL, LTD. KOBELCO: Kobe
Kobe Steel is a leading manufacturer of rubber mixers, which are indispensable for the production of tires and rubber products.Our rubber mixers account for 40 percent of the global market share. Our state-ofthe Kobe Steel has developed coal-based direct reduction (DR) technologies, the FASTMET, FASTMELT and ITmk3 processes, which reduce carbon composite agglomerates (pellets or briquettes) on the hearth of a rotary hearth furnace (RHF). This paper outlines the features of each process, status of technical development and commercialization. Also described Prospects for Coal‑based Direct Reduction Process
احصل على السعر
Press Release Details The former Nippon Steel Press
Outline of the Joint Company. Company name: Nittetsu Shinko Metal Refine Co., Ltd. Capital Ratio: Nippon Steel 70%, Kobe Steel 30%. Location: On the grounds of the Nippon Steel Hirohata Works. (Fuji-cho, Hirohata-ku, Himeji, Hyogo Prefecture) Capital Investment: Approximately 20 billion yen. (Investment will be primarily for a rotary Midrex Technologies and Kobe Steel, Ltd. has also developed the Fastmet process. This is a coal-based reduction technology, applicable to both steel mill waste and iron ore fines, with coal as a C-reductant agent. The reduced iron can be fed to a BF or directly into a melting process. Rotary hearth furnace: Coal: 100Direct Reduction an overview ScienceDirect Topics
احصل على السعر
Current status of the technology for utilizing ScienceDirect
The pyrometallurgical process enriches the dust and sludge with valuable elements, such as In and Sn, in the Zn-rich dust (hereafter collectively referred to as secondary dust). The chemical compositions of secondary dust from a steel plant rotary hearth furnace (RHF) and rotary kiln are shown in Table 3. The conventional treatment Hiroshi Sugitatsu is an academic researcher from Kobe Steel. The author has contributed to research in topics: Direct reduced iron & Slag. The author has an hindex of 9, co-authored 35 publications receiving 164 citations. The briquette is charged in a rotary hearth furnace together with the large lumps, and heated in the furnace to removeHiroshi Sugitatsu Kobe Steel 35 Publications 164
احصل على السعر
Review Future Steelmaking Model by Direct Reduction
Research and Development Dept. Iron Unit Division, KOBE STEEL, LTD., 4-2-7, Iwaya-Nakamachi, Nada-ku, Kobe, 657-0845 Japan. (rotary hearth furnace) to produce the iron nuggets. Figure 5 shows the process flow of the ITmk3 process. Since high strength is not required for processing in theCorpus ID: 136504774; Rotary hearth furnace technologies for iron ore and recycling applications @article{Ishikawa2008RotaryHF, title={Rotary hearth furnace technologies for iron ore and recycling applications}, author={Hideki Ishikawa and John T. Kopfle and James M. McClelland and Jenna Ripke}, journal={Archives of Metallurgy and Materials}, Rotary hearth furnace technologies for iron ore and recycling
احصل على السعر
NZ504325A Rotary hearth furnace with roof burners for
A rotary hearth furnace for reducing metal oxides using coal includes roof burners 5. The metal oxide coal mixture 6 is heated to produce flammable gases. The initial heating is carried out by roof burners 5, which produce a strong stirring action to mix the flammable gases and an oxidising gas. The roof burners are used in zones 1 and 2 of the furnace, RHF tech leader over 80 per cent of the Chinese market share. CISDI Thermal Engineering and Environmental Protection Co. is making great strides in converting steel production to greener processes. It has now built nine rotary hearth furnaces at Yanshan Steel, Baosteel Zhanjiang, Shanghai and Wuhan, Shougang Jingtang and Specialised Topic: CISDI’s state-of-the-art RHF tech creating greener
احصل على السعر
Method of operating a rotary hearth furnace Google Patents
To provide an operating method of a rotary hearth furnace for producing reduced iron in which a stuck substance stuck on the hearth surface is removed from the hearth surface to thereby prevent or reduce the wear of the knife edge of a screw of a discharge device, enabling continuous operation for a long period and capable of achieving high availability Abstract. Production of direct reduced iron from indigenous raw materials is an attractive alternative to the use of scrap for electric steelmaking or for a DR-based integrated steel plant. The SL/RN process is a proven coal-based direct reduction technology, its versatility being characterised by flexibility in the use of raw materials (lumpSL/RN coal-based direct reduction the state of the art
احصل على السعر
Nippon Steel and Kobe Steel to Establish Joint Company for Steel
Capital Ratio: Nippon Steel 70%, Kobe Steel 30% Location: On the grounds of the Nippon Steel Hirohata Works (Fuji-cho, Hirohata-ku, Himeji, Hyogo Prefecture) Capital Investment: Approximately 20 billion yen (Investment will be primarily for a rotary hearth furnace-type reduction furnace and related equipment.The rotary hearth furnace appears to be the most suited separation technique available due to its lack of sensitivity to zinc present in zinc ferrite compounds, and reintegration of the recovered iron into the steelmaking process. McClelland et al. reported on the chemistry of typical input and output material to Kobe Steel's KakogawaThe chemical suitability for recycling of zinc ScienceDirect
احصل على السعر
Development of Rotary Hearth Furnace Semantic Scholar
The ironmaking technology of rotary hearth furnace and its development abroad are introduced and discussed in this paper comprehensively,including INMETCO and the development from Fastmet to Fastmelt,IDP(developed by US Steel Dynamic Inc),as well as polytechnics of COMET,REDSMELT and DryIron,and also the so-called Itmk-3(third Kobe Steel has developed coal-based direct reduction (DR) technologies, such as FASTMET, FASTMELT and ITmk3, where carbon composite agglomerates (pellets or briquettes)are placed on the hearth to be processed with (解説) 石炭ベース還元プロセスの展望 KOBELCO
احصل على السعر
Isao Kobayashi's research works Kobe Steel, Kobe and other
Composite pellets or briquettes also find use as the feed material for new generation iron-making technology such as Fastmet [2, 3] or ITmk3 [4], which uses a rotary hearth furnace-based process2. The midrex/kobe steel RHF concept To be successful, rotary hearth furnace direct re-duction must be properly applied for each case, whether greenfield or at an existing facility. If so, the result is an energy-efficient, environmentally-friendly, economic system for producing quality alternative iron. The Midrex/Kobe Steel RHF concept has beenROTARY HEARTH FURNACE TECHNOLOGIES FOR IRON
احصل على السعر
Rotary hearth furnace technologies for iron ore and recycling
@misc{etde_21073760, title = {Rotary hearth furnace technologies for iron ore and recycling applications} author = {Ishikawa, H, Kopfle, J, McClelland, J, and Ripke, J} abstractNote = {Midrex Technologies and Kobe Steel offer the FASTMET, FASTMELT, and ITmk3 Technologies for processing iron ore and iron-containing by-products to produce Sahoo S, Sarkar S et al (2019) Role of scrap recycling for CO 2 emission reduction in steel plant: a model based approach. Steel Res Int 90:1–11. Google Scholar Halder S, Fruehan RJ (2008) Reduction of iron-oxide-carbon composites: part II. Rates of reduction of composite pellets in a rotary hearth furnace simulator.Review on Reduction Kinetics of Iron Ore–Coal Composite
احصل على السعر
FASTMET® Process Products || KOBE STEEL, LTD.
FASTMET ® is a direct reduction process using rotary hearth furnace (RHF). Various carbon sources such as coal, coke breeze or carbon bearing wastes can be used as reductant. Reduction process is completed in 6 12 minutes. Kobe Steel, Ltd. (Kakogawa Works) 16,000 tpy: April, 2001: Nippon Steel & Sumitomo Metal (Hirohata Works No.2
احصل على السعر- محطة إثراء خام الحديد للإيجار
- معلومات عن المعادن
- TON mill dia 4 6 11 35 mtr egl
- الصخور والمعادن التي تصنع الصخور
- أستراليا مخروط محطم
- إنتاج نبات التكسير المستخدم
- descargar gold extraction e book
- پارامترهای فرآیند برای آسیاب غلتکی عمودی
- الات الترصيص الصحي
- موزعين آلة تكسير الحجر المتنقلة الهند
- vibrating feeder 1600 tons per hour
- سحق السعري مصنع
- القياسات النباتية كسارة الفك الهند
- وكلات المعدات الثقيله مثل الشويل والت
- China Crusher 2006 Models Concrusher Detials