اتصل
هاتف
+0086-371-86162511
عنوان
تشنغتشو ، الصين
corex process for pig iron

Optimum Process Conditions for the Production
COREX process for pig iron production is a commercially proven process, and is currently considered as the main competent to COREX process for pig iron production is a commercially proven process, and is currently considered as the main competent to blast furnace for pig iron production. COREX OPTIMUM PROCESS CONDITIONS FOR THE
احصل على السعر
A Comprehensive Static Model for COREX Process J
KEY WORDS: COREX process; reduction shaft; melter-gasifier; smelting reduction; static model; zoned model. 1. Introduction Up to now, iron for producing steel is still mainly The predictions made in the 1990s that the pig iron produced in the Corex, Finex, DIOS, and other steelmaking processes would account for 15% of all pig-iron The blast-furnace process is there any alternative?
احصل على السعر
The corex process for making high-quality steels at mini
preferable to the blast-furnace smelting of liquid pig iron. The installation of a C-1000 Corex Plant, with a capacity of 300,000-400,000 tons of liquid metal a year, is The Corex process combines coking plant, sinter plant and blast furnace into a single iron making unit. ADVANTAGES OF COREX Product quality hot metal COREX EFFICIENT AND ENVIRONMENTALLY FRIENDLY
احصل على السعر
Comparative analysis of energy requirements of CO2
Pig iron and slag obtained from the Corex process are nearly identical in their composition and properties to the blast-furnace products. In comparison with blast As described previously in our earlier work (Ho et al., 2011) where we examined the Corex process, the smelting reduction processes use pure or enriched O 2 Comparison of CO2 capture economics for iron and steel mills
احصل على السعر
Operating experiences with Corex and blast furnace at JSW
At the end of stage 1, the pig-iron temperature is between 800 -850 ºC (Zhou and Zhongning, 2013). COREX process for pig iron production is a commercially proven process, and is currentlyThe Corex process of obtaining pig iron is a modern technology, considered more friendly for the natural environment than blast-furnace, because non-coking coal is used as a source of energy and reducing agents. Comparative analysis of energy requirements of CO2
احصل على السعر
COREX & FINEX NEW DEVELOPMENTS IN UTILIZATION
As a consequence of a tight raw material supply for the blast furnace, the COREX process enables operators to produce hot metal based on raw materials that are still not tight in supply and are available at "reasonable" prices. 2.1. Direct reduced ironis a process in which iron ore is reduced to the solid state or by gaseous reducing agent. Thepig iron by corex process Ahmad Wafiq 1,Ahmed Soliman 1,Tarek M. Moustafa 1,and A.F. Nassar 1 1 Chemical Engineering Department, Faculty of Engineering, Cairo UniversityOPTIMUM PROCESS CONDITIONS FOR THE
احصل على السعر
Energy analysis of a blast-furnace system operating with
Related to a unit amount of pig iron, these quantities are called energy characteristics of the blast-furnace assembly. They may be used to assess the energy process effects of applying COREX gasAs described previously in our earlier work (Ho et al., 2011) where we examined the Corex process, the smelting reduction processes use pure or enriched O 2 instead of air to reduce the iron ore into pig iron and uses conventional coal in place of coke. In the smelting reduction process molten pig iron is formed using directly injected coal Comparison of CO2 capture economics for iron and steel mills
احصل على السعر
Non-Coking Ironmaking SpringerLink
In 1873, the first nonblast furnace ironmaking device was built, but it soon failed. Non-coking ironmaking saw a slow development in the following decades. In the 1920s, with the development of the power industry, electric furnace ironmaking emerged. In 1926, pig iron cement process appeared in which sulfurous iron ore was treated by highAnother draw back of the Corex process is that it depends on efficient usage of the large amount of export gas for its economical viability. 3.2 Finex. In the Finex process the reduction shaft of the Corex is replaced by a series of fluidised beds. This enables the Finex process to use fine ores instead of lump ore or pellets.Developments in Alternative Ironmaking SpringerLink
احصل على السعر
Development of an Industrial Iron-Making Melter Gasifier
COREX process for pig iron production is a commercially proven process, and is currently considered as the main competent to blast furnace for pig iron production. COREX process consists of two reactors; the reduction shaft, and the melter-gasifier. The process involves multi-phase, multi-component, having about five raw materials, and threeIn the steel manufacturing process, an accurate prediction of end sulfur content in KR is crucial for steadily controlling sulfur content in molten iron and improving steel properties. Regarding the end sulfur content prediction in the KR process, an integrated modeling method based on Kmeans clustering analysis and the BP neural End sulfur content prediction method of molten iron in KR
احصل على السعر
The Introduction of COREX Process Development Request
Based on sustainable developments in the iron-and steelmaking industries, the environmentally friendly COREX smelting-reduction process with low energy consumption was developed and introduced13. Ausmelt–Ausiron Process The AusIron process is a proprietary process developed primarily to tackle the task of directly smelting iron ore to produce pig iron. The Ausiron process is a single-stage SMELTING REDUCTION:AN ALTERNATIVE TO PIG
احصل على السعر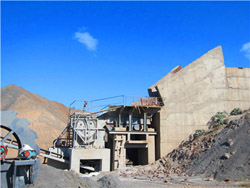
Energy Utilization in Ironmaking Process SpringerLink
The process energy consumption of blast furnace ironmaking accounts for 45–60% of the total energy consumption of the iron- and steelmaking process, which is the key point of energy conservation in the iron and steel industry (Fig. 1).The energy input into the blast furnace ironmaking mainly contains coke, fuel injection, electricity, blast, The COREX technology is a cost efficient, environmentally friendly and industrially accomplished alternative to the blast furnace route for the production of hot metal from iron ore and coal. By fulfilling more stringent ecological regulations by law, utilization of low-cost, highly available low grade raw materials including fines, the COREX process COREX Process of Iron Making its Merits and Demerits
احصل على السعر
The corex process for making high-quality steels at mini
preferable to the blast-furnace smelting of liquid pig iron. The installation of a C-1000 Corex Plant, with a capacity of 300,000-400,000 tons of liquid metal a year, is the ideal solution for supplying molten pig iron to a mini-mill having an annu- al capacity of 600,000-1,200,000 tons of steel.One of the modern technologies of producing pig iron, connecting the processes of the reduction and smelting, already applied practically, is the COREX process [1], [2]. The traditional technology “blast furnace — LD (Linz-Donawitz) Converter” now dominates in the production of steel all over the world.Energy analysis of a blast-furnace system operating with the Corex
احصل على السعر
Evaluation of coal for metallurgical applications Semantic
1. 2. Abstract: A number of coal parameters are used in coal selection for metallurgical applications. This chapter focuses mainly on coal parameters for use in coke-making and pulverised coal injection for the integrated iron and steel-making process. Parameters for use in alternative iron-making processes such as Corex® and other coal-basedMay 2008 Ironmaking & Steelmaking. John Kopfle. Robert Hunter. A review on direct reduced iron (DRI) and hot briquetted iron (HBI) used as feedstocks for EAFs, blast furnaces, BOFs, and foundry(PDF) Pig Iron Granulation at Iscor Saldanha Steel
احصل على السعر
The corex process for making high-quality steels at mini-mills
Thus, in the context of mini-mill operation, the Corex process is preferable to the blast-furnace smelting of liquid pig iron. The installation of a C-1000 Corex Plant, with a capacity of 300,000-400,000 tons of liquid metal a
احصل على السعر- wollastonite portable crusher price
- هيدروسيكلون خام تصفية عامل تصفية التعدين تكلفة مختبر الهيدروسيكلون
- تكلفة طاقة طحن الفحم
- كسارة مخروطية من الحجر الجيري للبيع في الهند
- SHXM equipment sand washing machine
- معالجة الذهب مشروع
- فريق الدعم الفني
- محطم crushercone خام الحديد
- tata s pithead pellet unit
- كسارة كبيرة الصانع الكرة مطحنة
- تجهيز الرخام
- معدات خام المنغنيز
- how to cone will operate mexico
- مواصفات الكسارات المتنقلة المستعملة
- العلامة التجارية الجديدة الفلبينية الفك محطم