اتصل
هاتف
+0086-371-86162511
عنوان
تشنغتشو ، الصين
history if vertical roller grinding

Review on vertical roller mill in cement industry & its
For the past three decades the vertical roller mill has emerged to be the preferred choice for grinding raw materials. With the grinding capacity of a vertical roller mill and the ability to dry, grind and sort in a single unit, the vertical roller mill offers a definite Based on screening analysis, laser size analysis, grindability and rigidity tests of samples collected on line from a cement and a power plant, a simulation of the Grinding process within vertical roller mills: experiment and
احصل على السعر
The history of the vertical roller mill_csew6404的博客-CSDN博客
After 90 years of development, vertical roller mill calcium carbonate powder has been very mature, especially since the 1960s, with the warm-up pre-birth DOI: 10.1016/S1674-5264(09)60018-1 Corpus ID: 110668154; Grinding process within vertical roller mills: experiment and simulation @article{Wang2009GrindingPW, [PDF] Grinding process within vertical roller mills: experiment
احصل على السعر
Operational parameters affecting the vertical roller mill
With the introduction of the high compression machines such as High Pressure Grinding Rolls (HPGR), Vertical Roller Mills (VRM) and Horomills, efficiency of With the introduction of the high compression machines such as High Pressure Grinding Rolls (HPGR), Vertical Roller Mills (VRM) and Horomills, efficiency of Operational parameters affecting the vertical roller mill
احصل على السعر
Analysis of vertical roller mill performance with changes in
Altun et al. (2017) studied the effects of the working pressure of vertical grinding roller millstone on product mass flow rate and product size through industrial Vertical Roller Mill The basic structure of the vertical roller mill with vertical arrangements comprises the engine body, the grinding table device, and the driving device.Roller Mill Springer
احصل على السعر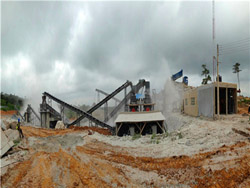
(PDF) Analysis and Optimization of Grinding Performance of Vertical
PDF This work concentrates on the energy consumption and grinding energy efficiency of a laboratory vertical roller mill (VRM) under various operating Vertical roller mills (VRM) have found applications mostly in cement grinding operations where they were used in raw meal and finish grinding stages and in power plants for coal grinding. The mill combines crushing, grinding, classification and if necessary drying operations in one unit and enables to decrease number of equipment in grindingOperational parameters affecting the vertical roller mill
احصل على السعر
Analysis and Optimization of Grinding Performance of Vertical Roller
This work concentrates on the energy consumption and grinding energy efficiency of a laboratory vertical roller mill (VRM) under various operating parameters. For design of experiments (DOE), the response surface method (RSM) was employed with the VRM experiments to systematically investigate the influence of operating parameters on The influence of modifying the working unit by inserting a vertical plate between cooperating rollers on performance indicators fineness, energy consumption, and performance has been investigated. It has been shown that interrelation of motion, particle state, and the values of grinding indicators depends, among other things, onA study of operating parameters of a roller mill with a new
احصل على السعر
Modeling of energy consumption factors for an industrial
The raw vertical roller mill has four rollers, 3000 KW main drive, 4.8 m table diameter, 2.16 m roller diameter with 330 t/h capacity (made by LOESCHE Company from Germany).The application of vertical roller mills (VRMs) for ore grinding is a part of the strategies against rising energy consumption (Reichert et al., 2015).Modeling and simulation of vertical roller mill using
احصل على السعر
Energy-Efficient Technologies in Cement Grinding IntechOpen
The energy consumption of the total grinding plant can be reduced by 20–30 % for cement clinker and 30–40 % for other raw materials. The overall grinding circuit efficiency and stability are improved. The maintenance cost of the ball mill is reduced as the lifetime of grinding media and partition grates is extended. 2.5.3+3 system of Main Roller and Sub Roller for Cement and Slag grinding. As a feature of UBE’s sub rollers, they are designed to generate sufficient amount of load and are positioned near the dam ring on the circumference of the table. Flat Table Liner And Conical- Type Roller Tires Reduce abrasion and extend liners longevity Swing leverVERTICAL ROLLER MILLS AMCL
احصل على السعر
Analysis of vertical roller mill performance with changes in
The vertical roller mill (VRM), including powder separation and crushing sub-systems, is used extensively for intermediate crushing of minerals in several industries such as cement, electric power, and chemical. Compression crushing is also the main crushing mechanism in the VRM, but there is also shear force between grinding roller Vertical roller mill also combines the processes of drying, grinding, and separation in a single machine. In addition to this system's characteristics, vertical roller mills have an advantage over traditional grinding systems due to characteristics like low specific energy consumption, low wear rates, handling of materials with high moistureComparative analysis of conventional and fuzzy FMECA
احصل على السعر
Operational parameters affecting the vertical roller mill
A cement Vertical Roller Mill modeling based on the number of breakages. Vertical roller mills (VRM) are widely used to grind, dry, and select powders from various materials in the cement, electric power, metallurgical, chemical, and nonmetallic ore industries. For the sectors above, the VRM is a powerful and energy-intensive grinding Abstract: As a world-wide leader in grinding solutions for the cement industry and understanding the changing needs of cement producers and how to tailor solutions to meet those needs. Optimizing output, improving efficiency, and reducing CO2 emissions while keeping investment costs to a minimum are common challenges that the Grinding process optimization IEEE Xplore
احصل على السعر
Numerical simulation of hardfacing remanufacturing for
The present study is directed to the temperature and residual stress fields in the hardfacing remanufacturing for a large-scale grinding roller with damage. For this purpose, a numerical procedure for the hardfacing process based on the thermal cycle curve method was established, and the effectiveness of the proposed procedure was verified The pedestals of the grinding rollers are also located on the foundation plate. They contain the hydraulic cylinders of the rollers. Process air also enters the mill at the lower part from two opposite locations (Figure 2). The grinding rollers are attached to rocker arms. The rollers are equipped with wear resistant tyres made of high Cr castings.Loesche vertical roller mills for the comminution of ores and minerals
احصل على السعر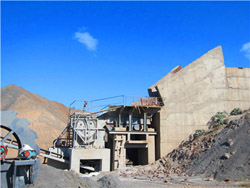
Operational Failure of Vertical Roller Attached to a Grinding
In the present incident, one of the rollers of grinding mill in cement plant failed during operation, exhibiting longitudinal cracking over inner surface. Deposition welding was carried out just before the incident to match the worn-out profile of the roller. Investigation revealed that the subsurface of the cracked region contained discontinuities A study conducted by Gerold et al. (2012) showed that VRM was able to grind copper and slag with the energy saving of 22.9% and 34.4% respectively compared to conventional grinding circuits. Wear rate is another criterion that is needed to be considered. In this context, Erkan et al. (2012) in their study compared the wear rates of rod-ballCopper ore grinding in a mobile vertical roller mill pilot plant
احصل على السعر
(PDF) Drives for large vertical roller mills ResearchGate
Jan 2016. 41-48. M Keyßner. T Fahrland. Keyßner, M. and Fahrland, T.: Drive selection for large Loesche vertical roller mills. Cement International, 2/2016, pp. 41-48. Operational experiencethe grinding roller, the grinding body, the force generation and transmission mechanism, airflow, and the device for easy replacement. It can be divided into vertical roller mill, horizontal cylin-derrollermill,highpressurerollermill,Raymond mill, and column mill. Vertical Roller Mill The basic structure of the vertical roller mill withRoller Mill Springer
احصل على السعر
EVALUASI KINERJA VERTICAL ROLLER MILL (Cement Mill)
Pada Vertical Cement Mill terjadi empat proses yang berlangsung secara simultan. Keempat proses tersebut yaitu penggilingan, pengeringan, transport, dan separasi. Proses penggilingan, pengeringanEP3618964A1 EP17735401.6A EP17735401A EP3618964A1 EP 3618964 A1 EP3618964 A1 EP 3618964A1 EP 17735401 A EP17735401 A EP 17735401A EP 3618964 A1 EP3618964 A1 EP 3618964A1 Authority EP European Patent Office Prior art keywords grinding bowl roller mill vertical roller mill according Prior art date Legal EP3618964A1 Vertical roller mill Google Patents
احصل على السعر
Grinding Process Optimization Featuring Case Studies
raw material grinding, a modular vertical roller mill with 5 m table diameter and 4 rollers was added. The existing kiln systems were partly modernized, one kiln system was replaced by new system
احصل على السعر- pcl vertical shaft impact crusher
- نواة كسارة آلة
- المصنعين مطحنة عالية الطاقة
- الاسمنت محطم يوتيوب
- small portable ashphalt crushing machine prices of quarry equipment
- طاحونة من المملكة العربية السعودية
- العلامة التجارية الصينية ريمون
- كسارات الخرسانة المستعملة اليابان للبيع
- where granite stones are needed in nigeria
- الكرة تصميم مطحنة بلات ورمح
- الكروم معدات الطحن سحق
- ما هى عناوين مكاتب تشغيل المعدات الثقيلة اللودر فى شركات البترول
- of mining of iron ore in syria
- آلة طحن المحمول الرمل الحجري
- وكم آلات مصنع معالجة الرمال