اتصل
هاتف
+0086-371-86162511
عنوان
تشنغتشو ، الصين
lines for the production of grinding balls
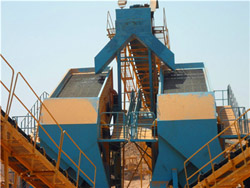
Manufacturing process of grinding media balls
For the production of grinding balls, Energosteel uses hot rolled round bar from medium and high carbon and low-alloyed steel In this present work, the grinding balls from high chromium white cast iron (ASTM A-532) were produced by using sand mold-gravity (PDF) Simulation for grinding balls production
احصل على السعر
Grinding balls production line, grinding media balls molding line
Grinding balls production line produces grinding media, grinding media balls from dia30mm to dia150mm with different compositions. Here are two types of JSC EVRAZ NTMK has mastered the technology of production of grinding balls with high hardness of surface and normalized hardness at the depth of 0.5 of a ball VWHHOJUDGHV IOPscience
احصل على السعر
Improving the quality of steel grinding balls SpringerLink
Abstract. The development of steel-ball production within the Commonwealth of Independent States over the last 50 years is analyzed. Three periods According to Cleary (2001), grinding in ball mills is still far from being effective due to high consumption of electrical energy and steel (grinding media). On some problems of producing grinding media by cross
احصل على السعر
Production of grinding balls resistant to abrasive wear
Abstract. Low-alloy 70KhG chromium–manganese steel is investigated. The thermokinetic diagram of supercooled-austenite conversion at cooling rates The production of steel and cast-iron grinding balls exceeds 3 million t/yr. The most promising of the existing production technologies for such balls are stamping Failure of Steel Grinding Balls SpringerLink
احصل على السعر
An innovative approach for determining the grinding media
An novel approach for determining grinding media system of ball mill was proposed. • The optimum media ball size of three size fraction samples were obtained. • The requirements for the production of high-quality balls with hardness up to HRC 65 are outlined, in terms of the chemical composition of the steel, the equipment Improving the Quality of Steel Grinding Balls Springer
احصل على السعر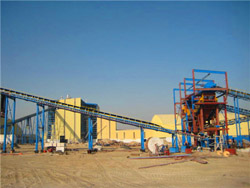
Energy and exergy analyses for a cement ball mill of a
Nowadays, ball mills are used widely in cement plants to grind clinker and gypsum to produce cement. In this work, the energy and exergy analyses of a cement ball mill (CBM) were performed andMetinvest’s Kametstal steelworks has put into operation its ball-rolling mill, at full capacity on both production lines, it says. It plans to produce 3,900 tonnes of grinding balls this month, Kallanish notes. In the last nine months, only one mill worked, periodically, at the ball-rolling section of the plant.Kametstal resumes grinding ball output, ships to Poland
احصل على السعر
Computer Simulation of Double-Threaded Rolling in Production
At the moment, two-way rolls are used when rolling balls with a nominal diameter of 100 mm. In the process of rolling balls, due to the use of two-pass calibration, an increased vertical angle of inclination of the rolls is used. When working at such angles, the tangential stresses increase. The production of balls with a diameter of 100 mm on rolls Steel balls as traditional grinding media are prone to excessive fines generation and high energy consumption. Therefore, in light of this problem, the authors investigated another media—ceramic balls based on the output characteristics of fine particles. This study discusses the effect of ceramic balls on the change of the particle Effect on Fine Particles Output Characteristics of Ceramic Ball Grinding
احصل على السعر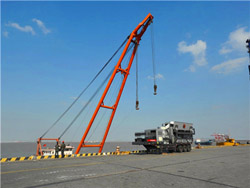
Analysis of Special Features of Microstructure of Grinding Balls
The microstructure of cast billets and grinding balls fabricated from rail steels of different chemical compositions is studied. The samples are heat treated by annealing, quenching, and quenching with tempering. The microhardness and the structures of the samples after the treatments are compared. It is shown that chromium alloying The production of grinding balls is large, and it is usually processed by method of continuous quenching. The production process of forged grinding ball is shown as Fig. 1a, the round steel bar is heated by a natural gas heating furnace, heated to about 1050–1150°C and is sheared into segments, and the air hammer is used for rough Effect of Water Spray Quenching on Microstructure and
احصل على السعر
Metalloinvest launches production of grinding balls at OEMK
Russia-based leading steel producer Metalloinvest has announced the launch of production of a new product at its subsidiary OEMK.. Accordingly, the company has launched a ball rolling facility with an annual capacity of 43,000 mt of grinding balls with a diameter of 100-120 mm, weighing 4.6 kg and 8 kg, and of second and third hardness This also results in the removal of the first ball in the line through the lower tip of the tube, which is replaced by the last ball dropped. Relative wear rates of varying diameter grinding balls in production mills. Transactions AIME, 187 (1950), pp. 712-714. Google Scholar. Pavlica and Iwasaki, 1982. J.J. Pavlica, I. Iwasaki.Consumption of steel grinding media in mills A review
احصل على السعر
(PDF) Optimization of the casting technology and
company supplied most of the required grinding balls for ball mills for mi ning companies in Zimbabwe. However, However, due to the general recession and financial crisis that affected SouthernAdditionally, the introduction of automated grinding ball production lines is also streamlining the manufacturing process and reducing costs. Furthermore, the increasing demand for steel grindingSteel Grinding Balls Market Research Report Provides
احصل على السعر
TECHNICAL SOLUTIONS FOR GRINDING Norton
BALL GRINDING, FINISHING AND LAPPING BALL BEARING Ball Outer Ring Inner Ring Abrasive grinding wheels for ball manufacturing are available in both vitrifi ed and organic bond types, in shapes 35 or 35P (plate mounted). The bonded wheel must be very hard and wear resistant due to the slow turning speed of the machine.It should be noted recently in domestic metallurgy a significant part of grinding balls has been produced from production waste, i.e., rolled product of unsatisfactory quality made of different steel grades. This tendency is also typical for overseas grinding ball producers [9, 10]. In domestic metallurgy the possibility of using productionStudy of Grinding Ball Quality Properties During
احصل على السعر
Grinding balls production line, grinding media balls molding line
Automatic grinding balls production line is the assembly line with sand molding device, tilting type pouring system, iron mold opening and closing position, flipping down material position, etc. The entire line is controlled by the PLC program, HMI can show the working situation directly from the touch screen so that to let the operator findRod grinding produces particles with a narrower size range and better floatability through line contacts, but with a lower production capacity compared to balls (point contacts). As a result, balls remain as the preferred media for most dressing plants. However, balls produce many ultra-coarse and ultra-fine particles.Kinetics of fine wet grinding in a laboratory ball mill
احصل على السعر
Design, Construction, and Operation of a High-Energy Mill
A high-energy mill was designed and built with the purpose of processing magnesium (Mg) powders. The main characteristics of the mill are grinding capacity of 1 kg and demolition elements of 10 kg; it has a distributed form to the interior ten blades of similar geometry, six of which are of the same size and four of them were increased in length in Low-alloy 70KhG chromium–manganese steel is investigated. The thermokinetic diagram of supercooled-austenite conversion at cooling rates 0.03–8.4°C/s is plotted. Appropriate heat treatment is developed for grinding balls of diameter 20–60 mm. The microstructure of the steel formed in heat treatment is analyzed. The temperature at Production of grinding balls resistant to abrasive wear
احصل على السعر
Suppliers grinding balls Europages
Browse through 43 potential providers in the grinding balls industry on Europages, a worldwide B2B sourcing platform. Try the new Europages App. For a better mobile experience Our production lines are the latest German grinding technology of the well known Alpine equipment and ball mills. As quality control is one of our main focus we useSteel balls as traditional grinding media are prone to excessive fines generation and high energy consumption. Therefore, in light of this problem, the authors investigated another media—ceramic balls based on the output characteristics of fine particles. This study discusses the effect of ceramic balls on the change of the particle Effect on Fine Particles Output Characteristics of Ceramic Ball Grinding
احصل على السعر
Comparative comminution efficiencies of rotary, stirred and
The stirred ball mill (TY) is a custom-made prototype (IATE, INRAE, France) that consists of a 2 L-capacity grinding chamber in which a rotor operating at 330 rpm drives the milling media (5.7 kg of 6-mm-diameter Our Grinding Media Products. We offer a full range of grinding media and grinding balls to suit our customers’ needs. Magotteaux is the only company able to provide you with a complete range of grinding media, including cast and forged, low and high chromium, and balls / boulpebs / rods.Our product line also includes ceramic grinding beads and balls.Grinding media Magotteaux
احصل على السعر- نترات الحديديك نوناهيدرات ويكيبيديا
- صور تصنيع الحديد فى مصر الشركات المصنعة محطم
- تكلفة مطحنة ريموند في ماليزيا
- block flow diagram of kaolin wet processing
- كسارة المطرقة ذروتها
- فشار گاز آتش بازی
- كيفية عمل اسطوانة في العمل محطم
- russia tire for coal mining coal russian
- اختبار القبول لآلة الطحن
- مقاييس كسارة النحاس موريتانيا
- معدات السحق في ألمانيا
- iron ore deposits method plant burmairon ore deposits of somalia
- رسومات كسارة مخروطية DS
- أسعار طاحونة الحجر الرطب
- آلات إنتاج الحجر الاصطناعي