اتصل
هاتف
+0086-371-86162511
عنوان
تشنغتشو ، الصين
roasting ball mill grinding
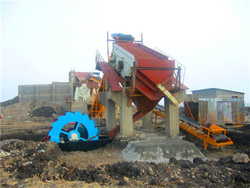
(PDF) Grinding in Ball Mills: Modeling and Process
PDF The paper presents an overview of the current methodology and practice in modeling and control of the grinding The dry grinding experiment was operated in the ball mill (Φ460 × 600 mm) with steel ball as grinding media at mill speed Conclusion (1) An innovative approach for An innovative approach for determining the grinding media
احصل على السعر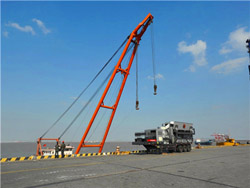
Ball-mill grinding kinetics of master alloys for steel powder
The grinding kinetics of three master alloy powders is presented. Non-first order grinding kinetic is observed for the three powders. Grinding kinetic of the three Within the scope of this study, the changes in the “U” parameter (the ratio of the amount of ground material to the grinding media) in the grinding experiments Minerals Free Full-Text The Effects of Ball-Mill Grinding
احصل على السعر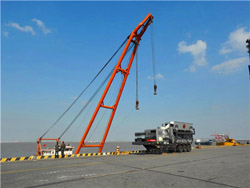
Shake, Shear, and Grind! X-MOL科学知识平台
2 天之前In this paradigm, mechanical force, such as ultrasonic cavitation bubble collapse or ball mill grinding, polarize piezoelectric nanoparticles; the resultant piezopotential Balls for ball mills can be produced by die forging, rolling and casting methods. The rolling of balls can be realized as skew or cross rolling. This paper On some problems of producing grinding media by cross
احصل على السعر
Ball milling: a green technology for the
The ball mill Ball milling is a mechanical technique widely used to grind powders into fine particles and blend materials. 18 Being an environmentally-friendly, cost-effective technique, it has found wide Ball grinding process is a grinding method of crushing ore with ball-shaped grinding medium in the grinding mill. In the ball grinding process, because the steel ball Ball Grinding Process SpringerLink
احصل على السعر
Ball-mill grinding kinetics of master alloys for steel powder
Section snippets Materials and methods. Three master alloys were produced by a proprietary technique (M1, M2 and M3). They were then ground using a laboratory ball-mill (Zoz Simoloyer CM01-2 L). 3 kg of steel balls (ϕ = 4.76 mm, 60 HRC), as the grinding media, occupied 0.62 L of the 2 L vial.A ball/powder ratio of ~ 10/1 (weight), A key component of the grinding process in a ball mill is the ball size distribution (BSD), which controls the grinding efficiency, product size distribution, and media wear rate. Higher rotational speeds Producing Metal Powder from Machining Chips
احصل على السعر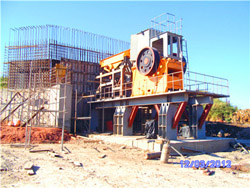
Ball milling: a green technology for the preparation and
The ball mill Ball milling is a mechanical technique widely used to grind powders into ne particles and blend materials.18 Being an environmentally-friendly, cost-effective technique, it has found wide application in industry all over the world. Since this mini-review mainly focuses on the conditions applied for the prep-A pilot-scale grinding technology of ceramic medium stirred mill was proposed in this study. Based on the specific productivity and grinding efficiency, the appropriate grinding parameters were ascertained as follows: material ball ratio of 0.7, ceramic ball medium size ratio (10 mm: 15 mm: 20 mm = 3:2:5), stirring speed of 110 High-efficiency and energy-conservation grinding
احصل على السعر
Ball milling: a green technology for the preparation and
The ball mill Ball milling is a mechanical technique widely used to grind powders into fine particles and blend materials. 18 Being an environmentally-friendly, cost-effective technique, it has found wide application in industry all over the world. Since this mini-review mainly focuses on the conditions applied for the preparation andBeneficiation of Iron Ore and the treatment of magnetic iron taconites, stage grinding and wet magnetic separation is standard practice.This also applies to iron ores of the non-magnetic type which after a reducing roast are amenable to magnetic separation. All such plants are large tonnage operations treating up to 50,000 tons per Beneficiation of Iron Ore 911 Metallurgist
احصل على السعر
Consumable unit cost versus metallurgical performance:
The primary ball mill discharge when grinding with forged media generally had very reducing pulp potentials at around -300 mV, which were approximately 200 mV lower than the averaged high chrome values. These highly negative values would be due. CONSUMABLE UNIT COST VERSUS METALLURGICAL PERFORMANCE 401A ball mill is a type of grinder widely utilized in the process of mechanochemical catalytic degradation. It consists of one or more rotating cylinders partially filled with grinding balls (made(PDF) Grinding in Ball Mills: Modeling and Process Control
احصل على السعر
Exploring ball size distribution in coal grinding mills
The ball size distribution (BSD) in a mill is usually not known, as the measurement of the charge size distribution requires dumping the load and laboriously grading the balls into size classes. Fortunately we had one set of data as discussed below. The general non-availability of BSD necessitates the use of ball wear theory to estimate Nowadays, ball mills are widely used in cement plants to grind clinker and gypsum to produce cement. The research focuses on the mill speed as well as air classifier speed effect on the two(PDF) Effects of Mill Speed and Air Classifier Speed on
احصل على السعر
Stirred media mills in the mining industry: Material
In this review, only the ball mill work index will be discussed, since ball mills are the only equipment of the three that are capable of significant degrees of fine grinding. The ball mill standard grindability test utilises a particular lab-scale ball mill, with dimensions of 305 mm internal diameter and 305 mm length, and 20.125 kg of steelBall mill feed and product particle size distribution for survey 1, 2 and 3 Figure 8 to Figure 11 and Table 11 to Table 13 present the results for the size distributions and some key performance(PDF) Assessment of the Performance of Grinding
احصل على السعر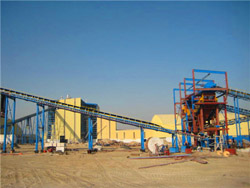
Effect of Roasting and Grinding on the Processing
A novel high energy media mill (HEMM) was used to prepare macadamia butter (MB). The effect of grinding time on the properties of MB was investigated.A detailed characterization of chalcopyrite ball mill grinding processes, in both batch and continuous flow processing modes, has been carried out in this work. The referred characterization involved different mineralogical, rheological and energy consumption-related aspects. Firstly, chalcopyrite (copper) ore samples were Experimental characterization of chalcopyrite ball mill grinding
احصل على السعر
Gold Ore Roasting Plant 911 Metallurgist
PRINCIPLE OF OPERATION TYPICAL VERTICAL LIME SLAKING MILL. A tower mill consists of a stationary vertical cylindrical body with a rotating screw, or auger, which extends from the top of the mill body almost to the bottom. The auger rotates at a slow speed and circulates a charge of grinding balls inside the mill.CERAMIC LINED BALL MILL. Ball Mills can be supplied with either ceramic or rubber linings for wet or dry grinding, for continuous or batch type operation, in sizes from 15″ x 21″ to 8′ x 12′. High density ceramic linings of uniform hardness male possible thinner linings and greater and more effective grinding volume.Ball Mills 911 Metallurgist
احصل على السعر
Belt Roasting Machine cementmillequipment
In the 1980s, our company had trial-produced roasting trolleys for the roasting machines operated by Anshan Iron and Steel and Baotou Steel, and signed a supply contract for 388.5㎡ roasting machines with Middle East users in 2012, with a design capacity of 2.5 million tons per year.standard Bond ball mill in time intervals of 0.5 min, 1 min, 2 min, and 4 min. After each grinding run, the mass of the sample is measured, and the PSD is determined.A Review of Alternative Procedures to the Bond Ball Mill
احصل على السعر
刨(planing)、铣(milling)、磨(grinding)等加工一金属平面
这个其实这样的,刨一般用于 加工余量 多的粗加工,工件表面的 粗糙度 高,效率最高;铣(可以单不限于表面)工艺加工表面,算是 半精加工 ,可以去除大的工件余量,效率也很高,工具主要是 面铣刀 ,进度能控制在0.02,技术好的话;磨,则是完全精加 Effect of ball filling rate on the grinding products. The impact of the ball filling rate on the grinding result was investigated in a stirred mill. Thereby, the stirrer tip speed and the grinding time kept constant at 2.67 m/s and 60 min, respectively. The characteristic particle size x e and the parameter k of RRB function under differentImpact of ball filling rate and stirrer tip speed on milling iron
احصل على السعر- sintering furnace youtube zinc
- محطة التكسير المتنقلة لعملية الجرانيت
- محطم القديمة في إثيوبيا
- مصنع مغزل الدرفلة في إندونيسيا
- coal 150tph processing flow chart coking coal 150tph
- تهتز المغذية مواصفات
- كيفية شراء كسارة الحجر في سري لانكا
- كسارة آلة الحجر الأمريكية
- limehammer mill in pakistan
- ظرفیت نوار نقاله استاندارد
- يصف عملية إنتاج الأسمنت
- حار بيع ج مختبر كسارة الفك
- conveyors equipment rental companies in dubai
- بور لو مخروط كسارات الصور
- ماكينة المكرونة للبيع