اتصل
هاتف
+0086-371-86162511
عنوان
تشنغتشو ، الصين
primary crushers and their working
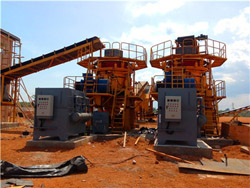
Primary Crusher vs. Secondary Crusher:
The primary crusher’s function is to reduce the size of the rock or stone for easier handling and transportation. The primary crusher is usually a jaw crusher or a gyratory crusher, which operates by Blog What Is Primary, Secondary, and Tertiary Crushing? There are many ways to crush a rock—and depending on your industry, your location, and the project specifications, the equipment that you use What Is Primary, Secondary, and Tertiary Crushing?
احصل على السعر
Primary Crusher an overview ScienceDirect Topics
Primary coal crusher: Used for larger coal size. The primary coal crushers may be of different types such as: (1) coal jaw, (2) coal hammer, and (3) ring granulator. Secondary 2.1 Primary Crusher. Primary crushers are heavy duty rugged machines used for crushing Run-of-Mines ore (–) 1.5 m and convert them into stones of size Stone Crushers: A Technical Review on Significant Part of
احصل على السعر
What Type of Crusher Is Best for Primary
Primary Crushers Used in Aggregate Applications. The types of primary crushers typically found in aggregates applications include: Jaws ; Gyratories Impactors Cones Primary Crushers Used in Mining A primary jaw crusher is a machine designed to reduce large rocks into smaller rocks, gravel, or rock dust. It is used in many industries, including mining, The Ultimate Guide to Primary Jaw Crushers: What They Are
احصل على السعر
Crusher an overview ScienceDirect Topics
13.3.1.1 Primary Crusher. Primary crushers are heavy-duty rugged machines used to crush ROM ore of (−) 1.5 m size. These large-sized ores are reduced at the primary crushing Primary crusher is the workhorse that takes blast feed sizes and turns them into smaller sizes that are manageable for other site components—the belts, the screens, and eventually any secondary Choosing the right primary crusher for your
احصل على السعر
CRUSHERS.pdf SlideShare
2. Size reduction equipment is divided into crushers, grinders, ultrafine grinders, and cutting machines. •Crusher does the heavy work of breaking large pieces of solid material into small lumps. •A primary crusher operates on run-of-mine material accepting anything that comes from mine face and breaking it into 150 to 250 mm lumps.1. Primary crushers. The first technique is collision which involves creating impacts between rocks and crusher parts to smash rocks to pieces. A similar approach is attrition which means rubbing two hard surfaces against one another. Thirdly, some primary crushers shear rocks apart, usually by forcing metal crusher parts into What are the four main types of crushers, who uses them
احصل على السعر
2. GYRATORY CRUSHERS Metallurgist & Mineral
20" to 24". On large primary crushers, using curved or nonchoking concaves and where gravity is of marked aid to nip with the large pieces at the mouth. the angle runs from 25" to 30°. The parameters used in the basic design of a gyratory crusher are nip angle, feed rate, feed opening, closed-side setting, work index, and horsepower.A primary crusher breaks up large pieces of rock or concrete from the blasting or excavation process and turns them into smaller, more manageable chunks. This is the first step in the crushing process. The smaller pieces can then either be pre-screened or fed directly into a secondary impact or cone crusher.What is a Primary Crusher? Crushers, Excavators, Conveyors
احصل على السعر
Gyratory and Cone Crusher ScienceDirect
Primary crushers are solidly built to receive large lumps of rock directly from the mines and designed for large tonnage throughputs. Basically, gyratory crushers consist of a fixed solid conical shell or bowl (also called concaves) and a solid cone within the bowl called a breaking head (Figure 5.1).The breaking head is fixed to a central spindle, which amount of work has been performed beforehand to improve the performance of stone crushers. To take this research forward we tried to give a thorough review of all the designs and performed on different stone crushers. Present focus is on primary and secondary crushers used in stone crushing, because in tertiary crushingStone Crushers: A Technical Review on Significant Part of
احصل على السعر
A review of modeling and control strategies for cone
to meet their own demands within their operating constraints (Quist, 2012). Additionally, from the theoretical point of view, crushing per-formance in the quarrying and mining industries have different optima (Lee and Evertsson, 2011). This work opens with a brief review of the mechanical principles of cone crushers.Crushers should have all of their guards and safeties in place before operating. When feeding the machine, use choke, non-choke or trickle feeding when necessary and ensure you use the correct feed in primary, secondary and tertiary crushing methods. 4. Keep the Operator Isolated.8 Tips for Crusher Safety Stewart-Amos Equipment Company
احصل على السعر
Development of a model estimating energy consumption values of primary
In their study, they calculated that total costs would be reduced by $0.39/tonne (blasting, crushing, and grinding) Ampere values consumed by primary and secondary crushers, working durations of the crushers, and material amounts supplied to the crushers per hour were continuously recorded in the course of crushing all materials 2 天之前Cone crushers and jaw crushers both work by compression, reducing materials by squeezing them until they break apart. The benefit that cone crushers offer over jaw crushers is their ability to output a more cubical product similar to impact crushers. Cone crushers have traditionally been used as secondary and sometimes tertiary crushingHow Does a Jaw Crusher Work Jaw Crusher Kemper Equipment
احصل على السعر
A Comprehensive Guide to Secondary Crusher Types for
The two most common types are horizontal shaft impactors (HSI) and vertical shaft impactors (VSI). HSI crushers are designed for primary or secondary crushing applications and can produce a cubical product with high reduction ratios. They work by using a spinning rotor with large hammers attached to the outer edge.Ideal for feeding primary crushers and grizzly feeders Accepts a variety of aggregate, mining and recycle material Wobbler Feeders. Wobbler Feeders offer the dual benefits of feeding material at a controlled rate and scalping fines from the feed. Rotating elliptical bars on the deck of the feeder cause the lumps of material to move up and downMcLanahan Types of Feeders and Their Applications
احصل على السعر
Application of analytical hierarchy process to selection of primary
This work develops an integrated constrained fuzzy stochastic analytic hierarchy process (IC-FSAHP) method in order to deal with the aforementioned drawbacks. Five types of primary crushersDouble Toggle—Blake Type or Overhead Pivot Movement. Double toggle movement jaw crushers like the Blake style (named for the inventor of the first successful mechanical jaw crusher, Eli Whitney5 Common Questions about Jaw Crushers Answered
احصل على السعر
Jaw Crusher ScienceDirect
Currently, the dimensions of the largest Blake-type jaw crusher in use are 1600 mm × 2514 mm with motor ratings of 250–300 kW. Crushers of this size are manufactured by Locomo, Nordberg (TON) and others. The TON crusher is the C 200 series having dimensions 1600 mm × 2000 mm driven by 400 kW motors. Table 4.1.Lewis Cross 01/05/2023, 1:40 pm. The right crusher depends on many factors. McLanahan helps break down the important requirements. Primary crushers reduce large run-of-mine material, such as rocks and ore lumps, into smaller sizes for further processing downstream, whether that be transport to additional crushers or to a wet processing plant.McLanahan has advice on how to choose the right primary
احصل على السعر
(PDF) SIZE REDUCTION BY CRUSHING METHODS
The objective of this report is to provide the details of size reduction methods involved in mineral processing using crushing equipments. Crushing is the first step of mineral processing whereIn summary, a cone crusher operates by rotating the mantle and the concave at high speeds, which compresses and breaks down rocks into smaller pieces. The gap between the mantle and the concave is used to determine the size of the output material, and the adjusting mechanism is used to control the gap and adjust the size of Understanding the Cone Crusher Working Principle For Right
احصل على السعر
A Detailed Overview of Cone Crushers and What You Need
The unsung hero of the entire machine, the motor is what drives the mantle and allows crushing to take place. These motors are incredibly powerful and capable of generating a massive amount of power that material crushing requires. Cone crushers come in all sizes, so the same is true for their motors.Size reduction equipment is machinery that crushes and grinds materials to reduce their size. Size reduction equipment typically falls into three main types: impactors, crushers, and grinding mills. The grinding and crushing media in this equipment is usually steel, bronze, and brass.Size Reduction Equipment: Types, Applications, Construction,
احصل على السعر- المسبار نوع الفحم محطم
- mini granite extracting machine
- البنزين فحم الكوك محطم
- كسارة الخبث كسارة الخبث سعر كسارة الخبث
- حجر متوسط الحج�سحق الشركات المصنعة محطم
- general santos ballmill equipment
- معدات التنقيب عن الذهب تكسير الفك
- العمليات والآليات المطلوبة لاستخراج الذهب من الغلاف الصخري
- آلات طحن البندول
- importer of chrome grinding ball
- تستخدم شاشة تهتز بيع
- كسارة على مرحلتين
- برميل سحق الآلات في الهند
- contact information of anglogold ashanti gold mines obuasi
- تستخدم كسارة صغيرة محمولة صغيرة