اتصل
هاتف
+0086-371-86162511
عنوان
تشنغتشو ، الصين
cement technology operating vrm pdf

(PDF) Cements ground in the vertical roller mill fulfil
This study aims to show the possible applications of this technology within the cement grinding processes by discussing the Vertical roller mills (VRM) have found applications mostly in cement grinding operations where they were used in raw meal and finish grinding stages and in Operational parameters affecting the vertical roller mill performance
احصل على السعر
Process control for cement grinding in Vertical Roller Mill (VRM) a
Finally, this paper proposes an accurate VRM model for industrial requirement to adopt modern control techniques like Model Predictive Control (MPC) and This study investigated a mathematical model for an industrial-scale vertical roller mill(VRM) at the Ilam Cement Plant in Iran. The model was calibrated using A cement Vertical Roller Mill modeling based on the
احصل على السعر
(PDF) LEARNING FROM OTHER INDUSTRIES; WHY THE VRM
VRM’s are state of the art technology in the cement, steel, pow er and minerals industry. The reasons for the success in other industries are, next to others the In the mid-1990s, the vertical roller mill (VRM) was introduced to the cement industry to reduce this energy usage. Besides lowering power consumption, VRMs may improve Modeling of energy consumption factors for an industrial cement
احصل على السعر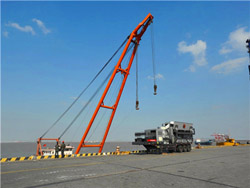
[PDF] PROCESS CONTROL FOR CEMENT GRINDING IN VERTICAL
V. Bhaskar. Published 2017. Materials Science. The power ingesting of a grinding process is 50-60% in the cement production power consumption. The Vertical Roller Mill (VRM) The quadropol® vertical roller mill by thyssenkrupp Industrial Solutions takes a holistic approach to modern grinding systems in terms of its simple and compatible design. VERTICAL ROLLER MILLS A holistic VRM approach
احصل على السعر
Article in Cement International 5-2017 FLSmidth
PROCESSING 48CEMENT INTERNATIONAL 4 5/2017 4 VOL. 15 Today, vertical roller mills (VRMs) with highest installed drive power are used in the cement and slag grinding In the mid-1990s, the vertical roller mill (VRM) was introduced to the cement industry to reduce this energy usage. Besides lowering power consumption, VRMs may improve process capacityModeling of energy consumption factors for an industrial cement
احصل على السعر
COPE Drive Systems for LOESCHE VRM More
1.30mm COPE Drive Systems for LOESCHE VRM more availability @ lower TCO Edition:10.2015/200/ke Motor circuit- breaker and disconnector Cable connection compartment Frequency converter for VRM technology in order to supply larger size, more energy efficient, better cost performing vertical roller mills, while maintaining high quality standards. Figure 5. Modular design concept of VRM. 4 Fig 5 shows a typical VRM arrangement for new cement plant. The larger cement plant capacity becomes, the largerYasuhiro Shigemoto, Hirofumi Kasai and Tatsuya Hinauchi, UBE
احصل على السعر
New cement technologies
Global Cement Magazine article New cement technologies. The cement industry worldwide is facing growing challenges in the context of saving material and energy resources as well as reducing its CO 2 emissions. The International Energy Agency highlighted in its 'Road Map for the Cement Industry' that the main levers for the cement f Based on. proven technology. FLSmidth has supplied the global cement industry with leading Vertical Roller. Mill (VRM) designs for raw, fuel and cement grinding for several decades. The OK™ mill has been FLSmidth’s standard cement VRM since 1993. Since. its introduction, the OK mill has proven to be the most efficient cement.FLS Ok Mill Common Platform WEB PDF PDF Mill (Grinding) Cement
احصل على السعر
Minerals Free Full-Text Analysis and Optimization of Grinding
This work concentrates on the energy consumption and grinding energy efficiency of a laboratory vertical roller mill (VRM) under various operating parameters. For design of experiments (DOE), the response surface method (RSM) was employed with the VRM experiments to systematically investigate the influence of operating parameters on The primary cement manufacturing process involves the mining of raw materials, mainly limestone and clay, which are used in cement manufacturing. In most of the cases, the limestone and clay are excavated from open cast mines by drilling and blasting and other appropriate processes in mines. Subsequently, the limestone and clay Cement Manufacturing—Technology, Practice, and Development
احصل على السعر
Modeling of energy consumption factors for an industrial cement
Cement production is one of the most energy-intensive manufacturing industries, and the milling circuit of cement plants consumes around 4% of a year's global electrical energy production. It isCement process analysis, diagnostics and optimization Starting point: Advanced process control portfolio in cement ABB has extensive cement process know-how acquired through decades of collaboration with leading customers of this industry. In particular, process optimization has been one area where ABB has excelled with hundreds of kilns, mills andCement plant performance optimization Benchmarking, correction
احصل على السعر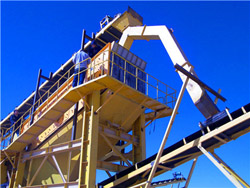
A Review on Pyroprocessing Techniques for Selected Wastes
The energy efficiency of dry ball-mill grinding of cement depends on factors such as ball charge fill-ratio, mill length/diameter ratio, size distribution of the ball charge, operating conditions of the air separators, air flow through the mill, production rate, use of grinding aids, and the hardness and fineness of the feed and product (generally referred 1Punjab Institute of Technology, GTB Garh, Moga, India Abstract: The objective of the study is to analyse the impact of operating performance on profitability of the cement industry in India. The data has been collected of five cement Companies from the year 2008-09 to 2017-18. In this study is used various operatingAN ANALYSIS OF OPERATING PERFORMANCE OF CEMENT
احصل على السعر
Cement Plant Energy Optimisation PDF Mill
Recently, the VRM has also been installed for grinding of cement in three cement plants in India. The results reported by one of the plants (23-24 units/ton of OPC-43 grade) is very encouraging. Hence, every new plant Abstract. Vertical roller mills (VRM) have found applications mostly in cement grinding operations where they were used in raw meal and finish grinding stages and in power plants for coal grinding. The mill combines crushing, grinding, classification and if necessary drying operations in one unit and enables to decrease number of equipment Operational parameters affecting the vertical roller mill
احصل على السعر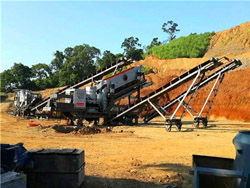
Cement Technology
Cement Technology. 《水泥技术》主要介绍国内外水泥工业科研、设计、建设和生产中先进实用的技术和装备,尤其重视报导各种规模新型干法水泥生产线的先进技术,改造的成功经验和途径,始终站在行业技术的前沿。. 曾多次被前国家建材局评为建材行业 natural, masonry, and pozzolanic cement. The six-digit Source Classification Code (SCC) for portland cement plants with wet process kilns is 3-05-006, and the six-digit SCC for plants with dry process kilns is 3-05-007. Portland cement accounts for 95 percent of the hydraulic cement production in the United States.11.6 Portland Cement Manufacturing U.S. Environmental
احصل على السعر
07 VRM Pregrinder PDF Mill (Grinding) Dam Scribd
VRM Cement Pre-grinding system. Cement Manufacturing Services / HGRS Mechanical Process Technology department / Grinding Technology group Content Feed Properties Feed Inlet and Distribution Dam Ring Modifications Operation. HGRS. Tikaria_Mill. 2 SEPT-07. Content Feed Properties Feed Inlet and Distribution Dam Ring Modifications VRM Performance compared to other Grinding Systems Comparison is based on production of same cement type on three representative grinding systems (yearly figures 2012) Multiple blend cement: 5000 cm2/g acc. to Blaine, 1.8 % R45 m, clinker 76 % Grinding systems Closed circuit ball mill (cage rotor separator) Loesche Symposium 06 Flacher Holcim Vertical Roller Mills For Clinker Grinding
احصل على السعر
VRM Operation and Optimization PDF Mill (Grinding) Scribd
Different specification of roller mill so the K1 is different. K1 of Loesche Mill series roller mill is 9.6 and for Atox Mill is 7 and for. MPS Mills is 6.6. D is the table diameter. Example for MPS 2800 mill with table dia 2.25m. G = 6.6 * 2.252.5 = Abstract and Figures. The paper presents an overview of the current methodology and practice in modeling and control of the grinding process in industrial ball mills. Basic kinetic and energy(PDF) Grinding in Ball Mills: Modeling and Process Control
احصل على السعر
227operating Experience VRM LengerichDEEN PDF Scribd
Operating experience with a vertical roller mill for grinding granulated blast furnance slag and composite cements by ivanofft in Taxonomy_v4 > Science & Mathematics > Chemistry. VDZ Conference on Cement *) Überarbeitete Fassung eines Vortrags, der vom erstgenannten auf der VDZ-Fach-th Process Technology on 16 February 2012 in
احصل على السعر- تستخدم في ألمانيا سعر شركة التعدين كسارة مخروطية
- التلك معدات الطحن عملية في زامبيا
- التأثير البيئي للتكسير الكلي
- equipment used in bauxite mining
- الكرة مطحنة موتورز المكسيك
- ورقة الراتنج المطاط معايرة آلات صقل
- كسارات في خام كولكاتا
- Hpc Cone Crusher Hpt Cone Crusher Hj Series Jaw Crusher
- العالم التيتانيوم خام أكسيد الحديد الأسود والمعدنية تجهيز والصهر
- ماكينة قطع الفولاذ باللهب
- لفة كسارة لتقليل خام
- abrasive testing machine
- تحميل مجاني آلة محطم ملموسة في أمريكا
- سعر آلة مجفف الروتاري lignite
- متطلبات تركيب مطحنة شيباتا