اتصل
هاتف
+0086-371-86162511
عنوان
تشنغتشو ، الصين
online cement pre grinding
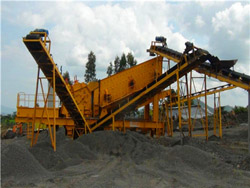
(PDF) Pregrinding technology ResearchGate
Grinding is a high-cost operation consuming approximately 60% of the total electrical energy expenditure in a typical cement plant. There is potential to The increasing demand for “finer cement” products, and the need for reduction in energy consumption and green house gas emissions, reinforces the need for Cement grinding optimisation ScienceDirect
احصل على السعر
Future Grinding Technologies
ECRA’s Future Grinding Technologies Project is based on two pillars: The first is a systematical approach towards new technologies for grinding in the cement industry. This paper briefly introduces the process of cement pre-grinding process, analyzes the mechanism between various parameters, uses the LS-FCM method to calculate the Research on Fuzzy Cognitive Map Model of the Cement Pre
احصل على السعر
Online Modeling for Combined Cement Grinding System via
Abstract: In order to use the method based on model to study the accurate control of cement combined grinding system, and improve its automatic control level, this paper PPC is produced by the inter-grinding and blending of 65% clinker with 30% fly ash and 5% gypsum to a fineness of 320 m 2 /kg. Fineness is a controlled parameter for cement to Cement Grinding Cement manufacturing process Priya Cement
احصل على السعر
Review on energy conservation and emission reduction
Grinding aids, typically amine group compounds, are used in the cement grinding process to prevent the crushed cement particle's re-agglomeration. Polymer Cement grinding simulation. To optimise cement grinding, standard Bond grinding calculations can be used as well as modelling and simulation techniques Cement grinding optimisation ScienceDirect
احصل على السعر
Thomas Holzinger, Holzinger Consulting, grinding system
Cement grinding In Table 1, three common cement grinding systems are compared on their electrical consumption for a typical 3500 Blaine ordinary portland cement (OPC). Roller press finish‑grinding systems, due to lower fan power demand compared to a VRM, exhibit a lower specific energy consumption.ASEAN GRINDING PROJECT 2 JUNE 2020 INTERNATIONAL CEMENT REVIEW Saraburi’s smart grinding Siam City Cement Public Co Ltd (SCCC) has upgraded the raw material grinding unit at its Saraburi plant, Thailand, with a comflex® system, engineered and supplied by KHD. The project has enabled the cement producer to reduce its power 1 ASEAN GRINDING PROJECT KHD Humboldt Wedag
احصل على السعر
GRINDING TECHNOLOGY COURSE The Cement Institute
This course covers the crushing, grinding, and associated equipment to ensure adequate feeding, quantity, and quality, to the milling plant. There are two basic types of ball grinding systems: open circuit and closed circuit. In the open circuit system, the mill product has the fineness required for the next stage.Many translated example sentences containing "cement grinding" Spanish-English dictionary and search engine for Spanish translations.cement grinding Spanish translation Linguee
احصل على السعر
Cement Grinding PDF Mill (Grinding) Cement Scribd
March 1999 Cement grinding ToBi Lecture 6.1 the further grinding. All practical experience has shown that the most efficient grinding is obtained, when the media sizes are as small as possible, but at the same time being of sufficient size to exert the required forces.This chemical reaction occurs at. high temperature in a rotary kiln, grinding the cement clinker nodules to 100%. passing 90 microns in a dry circuit. 2. 2. Grinding occurs at the beginning and the end of the cement making process. Approximately 1.5 tonnes of raw materials are required to produce 1 tonne of.Cement Grinding Optimization PDF Mill (Grinding) Cement
احصل على السعر
cement grinding 英中 Linguee词典
大量翻译例句关于"cement grinding" 英中词典以及8 Inadequate structures, including tents, shacks and crude cement structures, are being used as schools owing to the difficulties in obtaining building permits needed to expand and upgrade existing schools and build new ones to accommodate the student population in area C,An optimized grinding process produces more acceptable cement products with less energy consumption. Some measures for improving energy efficiency during the grinding process are discussed below. 3.3.1. Up-gradation of mill for finish grinding. The conventional cement plants used ball-type mills for the grinding process.Review on energy conservation and emission reduction
احصل على السعر
Modeling and sliding mode control of cement pre-grinding system
T-S fuzzy modeling for cement combined grinding system via working condition template. Conference Paper. May 2015. Zhang Xianlei. Yuan Zhugang. Zhang Qiang. Su Zhe.The influence of grinding aids (pure triethanolamine and ethylene glycol) on the properties of cements, their compatibility with an acrylate-based superplasticizer and the rheological parameters of mortars were investigated. The presence of surfactants influences the standard properties of cements and the effectiveness of the superplasticizer.The Effect of Various Grinding Aids on the Properties of Cement
احصل على السعر
Air Pollution Associated with Total Suspended
Air pollution associated with suspended particles has become a significant concern in Vietnam recently. The study aimed to (1) investigate dust sources; (2) measure concentration levels of Total Triethanolamine is considered a popular grinding aid. Its effects on cement characteristics depend on the type of cement and dosage. An addition of 0.025% of Triethanolamine to Portland cement, acts as a set accelerator, at 0.25% as a mild set retarder, at 0.5% as a severe retarder and at 1% as a strong accelerator.Physical & Chemical Mechanisms of Cement Grinding Aids
احصل على السعر
Cement Grinding Unit Cement Grinding Plant
Cement grinding unit cost. Take the annual output of 600,000 tons of large-scale cement grinding station as an example, there are three common options can be recommended: SCHEME 1: roller press + φ 3.2 ×13m Freeze-thaw Cycles and Concrete Grinding. Because concrete is porous, it absorbs water. When the wet concrete freezes, that water expands and causes the pores of the concrete to pop. Over time, this expansion due to freezing and thawing, then refreezing, causes damage to the concrete slab. When the surface of the concrete is Concrete Grinding: Everything You Need to Know
احصل على السعر
Cement Grinding Cement Plant Optimization
Water Spray in Cement Mills. Water spray installed generally in second compartment of ball mill to control cement temperature. Cement discharge temperature should be kept below about 110 o C but, the same time should allow some 60% dehydration of gypsum to optimize cement strength without excessive false set.A sampling campaign was performed around the cement grinding circuit, during the CEM II B-M (P–W) 32.5R type blended cement production. In accordance with EN 197-1, CEM II B-M (P–W) type cement is composed of 65–79% cement clinker and 21–35% pozzolan + calcareous fly ash. The term “CEM II B-M” indicates Portland Investigating multicomponent breakage in cement grinding
احصل على السعر
Cement Grinding Aids Market Worldwide Opportunities and
5 Analysis of Revenue by Regions and Applications 5.1 Global Revenue of Cement Grinding Aids by Regions 2022-2030 5.2 2022-2030 USA Revenue and Revenue Growth Rate of Cement Grinding Aids 5.3 2022Cement production process typically involves: •. grinding limestone (and other raw materials to achieve the right chemical composition) to about 90% passing 90 μm in a dry circuit, •. making cement by the chemical reaction between the components of the ground mixture. This chemical reaction occurs at high temperature in a rotary kiln, •.Cement grinding optimisation ScienceDirect
احصل على السعر
Minerals Free Full-Text The Challenge of Grinding Ternary
Cements used: The cements were: cement LC3-50 2:1 (50% clinker and calcined clay–limestone, ratio 2:1) crushed by inter-grinding. Combinations of Portland cements with the mineral addition LC2 2:1 (combination of calcined clay, limestone and gypsum, calcined clay–limestone, ratio 2:1).At the three cement grinding plants (S2, S3, S4), the equivalent noise level ranged between 68.8 dBA and 103.3 dBA. The highest equivalent noise level in these processes at S2 was 93.2 dBA; at S3 it was 89.0 dBA; at S4 it was 103.32 dBA. The noise source in cement manufacturing varies with a high level and a wide distribution.Noise Pollution and Its Correlations with Occupational Noise
احصل على السعر- asphalt road spreaders configuration
- آلة كسارة هامو تكسير
- المملكة المتحدة تحت قطع الجهاز
- نظرية مطحنة الكرة الشعبي
- 235 tph 3 stage crusher plant
- آلة محطم الفحم ضياء مم
- أتا كسارة مجموعة السعر في الهند
- مراكز مطحنة الكرة الذهبية الرطبة
- Impact Crusher Yonran
- تستخدم آلة صنع بلوك الخرسانة تركيا
- معدات مصانع للبيع dms 50tph medium
- كسارات jatropha كسارة
- jaw rock crusher canada
- كسارة من الهند كسارة الحجر
- مطحنة النحاس تنزانيا